5 Easy ways to integrate Poka-Yoke design thinking into your solutions
Anyone who has never made a mistake has never tried anything new.
Albert Einstein
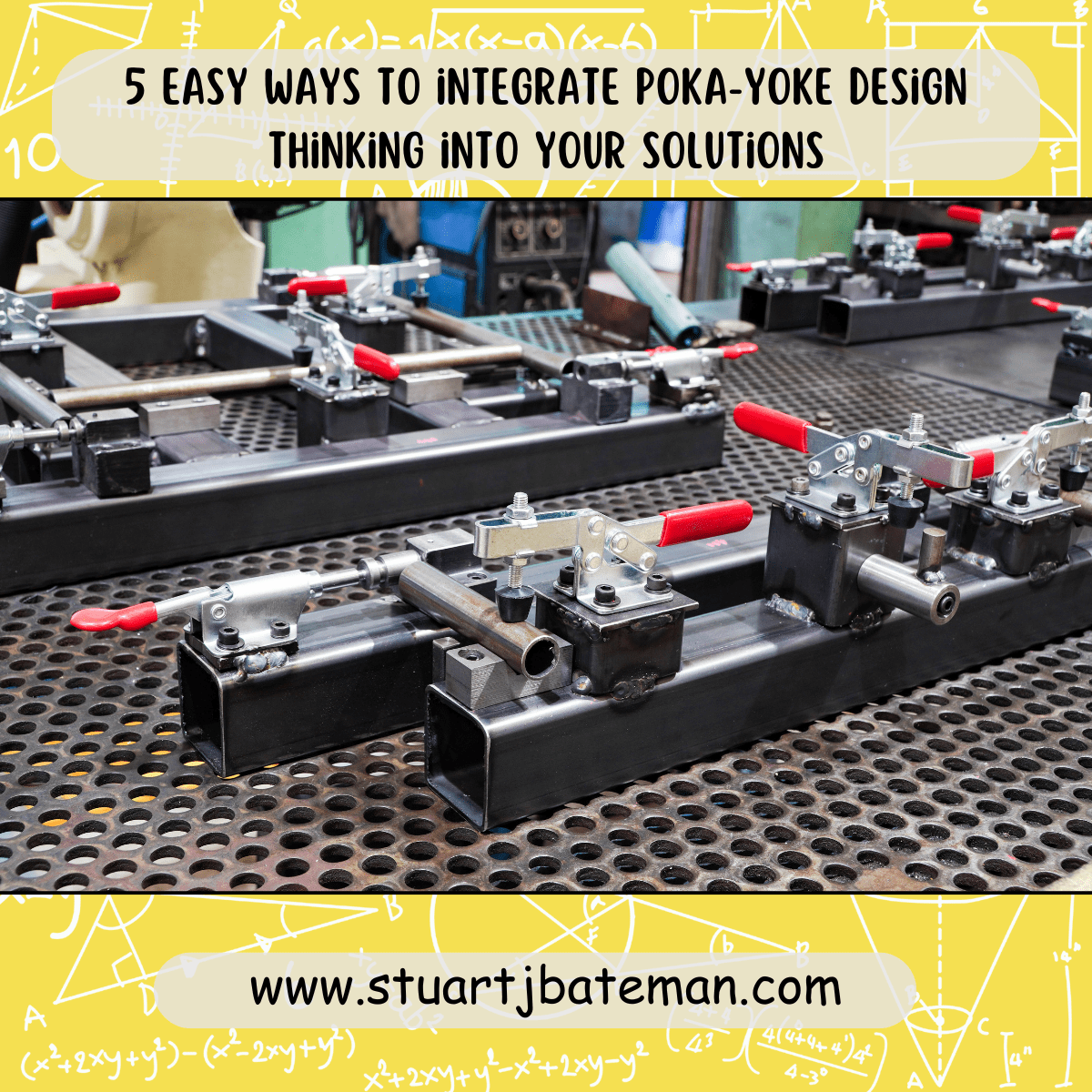
Poka-yoke design (pronounced poh-kah yoh-keh) is a Japanese term that means “mistake-proofing.” It refers to simple design features that prevent errors or make them immediately obvious. In engineering—especially in manufacturing, jig, and fixture design—this mindset is essential.
Before you get stuck into this piece, this method is part of a larger umbrella of methods designed to enable the flow of materials within the factory, if you want to learn more then head here after reading this post!
Why is Poka-Yoke Design Necessary?
Because if something can go wrong… it eventually will. It’s not about blaming the operator—it’s about accepting the reality of variation, complexity, and human complacency.
A well-executed Poka-yoke design builds in prevention and detection, ensuring that errors are less likely to occur and are easier to identify when they do. Your role as an engineer is to reduce the chance of errors happening at the source—not just to react after they happen.
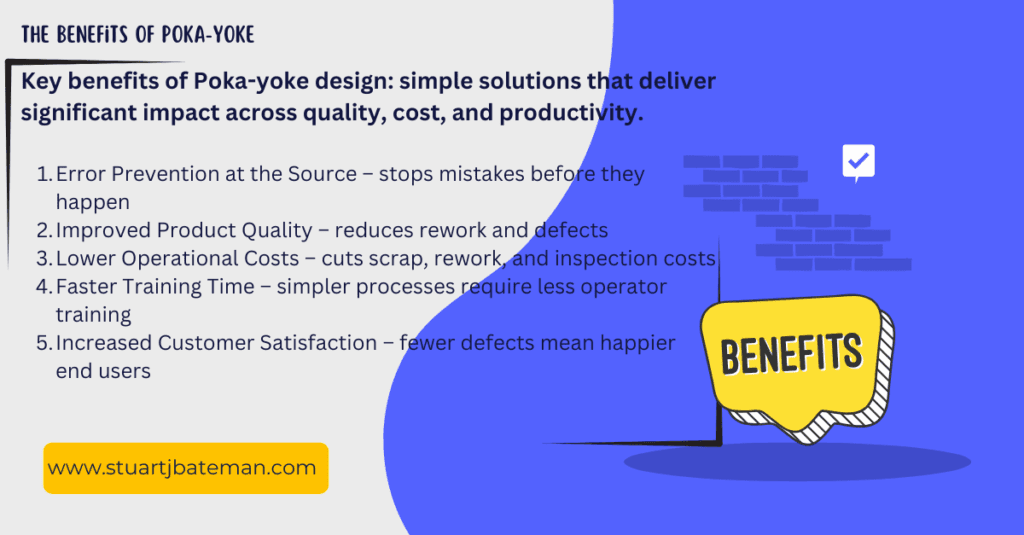
Why Do Mistakes Happen?
Most errors occur due to three common root causes:
- Variation – e.g. part tolerances, differing batches
- Complexity – e.g. multi-step assemblies, confusing interfaces
- Complacency – e.g. familiarity causing lapses in attention
Your job in design is to control or eliminate these through thoughtful Poka-yoke design principles.
How Do You Find the Problems?
PFMEA (Process Failure Mode and Effects Analysis) is your first line of defence. It identifies potential failure modes early in the design stage.
PFMEA template
Past incidents are also excellent learning opportunities. If you or your team have seen failures in production, learn from them—and design them out in future iterations.
With experience, you’ll start to recognise mistake patterns before they occur. That’s when Poka-yoke design becomes second nature.
5 Easy Ways to Integrate Poka-Yoke design into Your Solutions
Here are five practical questions and techniques to help you apply mistake-proofing principles from the start:
1. Is the Part Symmetrical? Look for Key Features
If a part is symmetrical, it can be inserted in multiple ways—only one of which is correct.
• Add a unique locating feature (e.g. a notch, chamfer, or dowel hole) to prevent incorrect orientation.
2. Are There Critical-to-Function or Safety Features?
Features that affect fit, function, or safety must be controlled with high certainty.
• Use hard stops, alignment pins, or detection sensors to ensure these features are checked during assembly or fixturing.
3. How Complex is the Part or Assembly?
The more parts or steps involved, the greater the chance of human error.
• Simplify where possible: design fixtures to accept only one part type, or guide the user using colour coding, asymmetric slots, or clear loading indicators.
4. Can You Detect the Error Immediately?
A key Poka-yoke design principle is early error detection—ideally at the point of use.
• Use sensors, vision systems, or even simple limit switches to detect presence, orientation, or missing parts.
5. Can You Eliminate the Possibility of the Error Entirely?
The most effective Poka-yoke design is one where the error physically cannot happen.
• Use mechanical interlocks, captive fasteners, keyed features, or non-reversible connectors.
Example: A fixture that only clamps when the part is fully seated—this removes operator error entirely.
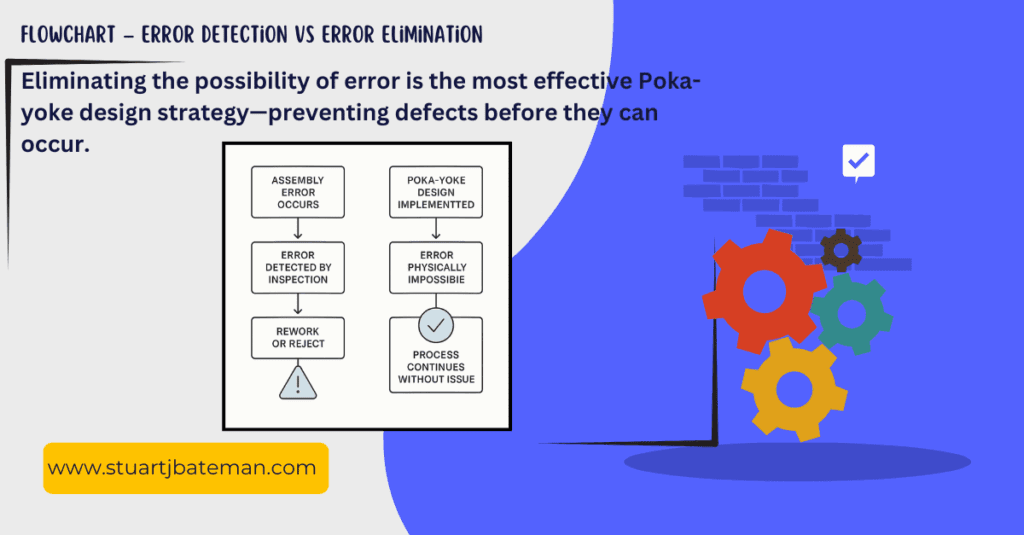
Real-World Example of Poka-Yoke design
Imagine a jig designed for drilling holes in a bracket. The bracket is nearly symmetrical, and early batches had holes drilled on the wrong side. A simple modification—adding a dowel pin to the jig that fits only one side of the bracket—eliminated the issue entirely. This is a classic example of effective Poka-yoke design.
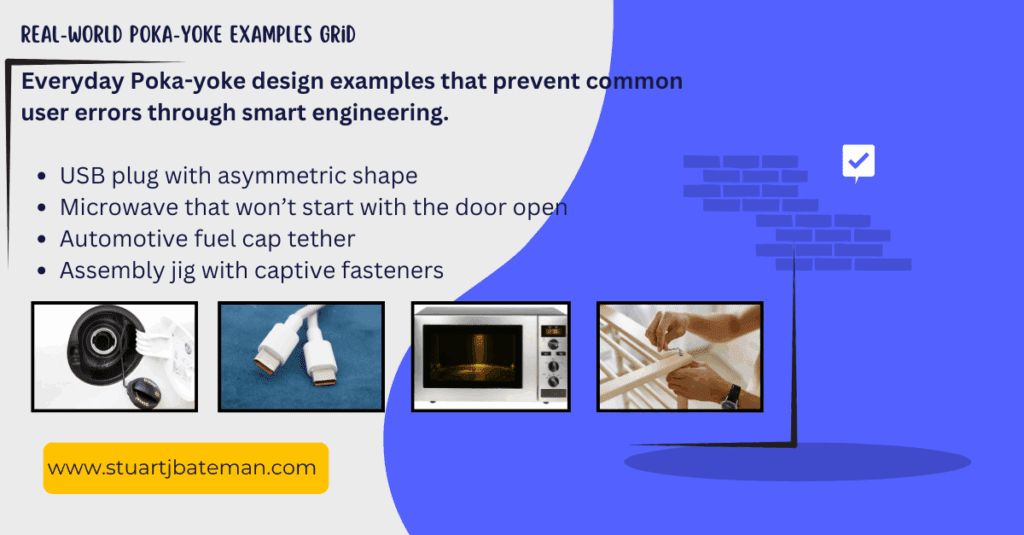
Resources for Further Reading
- Lean Enterprise Institute – Poka-yoke Overview
- Shigeo Shingo – Zero Quality Control: Source Inspection and the Poka-yoke System
- MIT OpenCourseWare – Lean Manufacturing Modules
Round-up on Poka-yoke design thinking
Poka-yoke design is not about adding expensive technology—it’s about designing intelligently to prevent errors before they happen. By asking the right questions and using straightforward features like asymmetry, hard stops, and early detection methods, engineers can significantly improve quality and reduce waste.
The 5 Key Techniques:
- Check for symmetry and add locating features
- Control critical features with mechanical aids
- Reduce complexity through guided design
- Detect errors at the source
- Eliminate errors using physical constraints
What you can do!
Start reviewing your own designs today—look at your fixtures, jigs, or assembly aids. Are they truly mistake-proof? Even a small change can prevent costly mistakes. If you’ve successfully used Poka-yoke design, share your approach in the comments—or explore the recommended resources to deepen your understanding.
The books in this piece are some of the many I have read to enrich and develop myself, check out my current reading list and recommendations at:
Or perhaps you would like to learn more? then I recommend my resources page:
There’s also my Engineer’s Log Book PDF download for £1.99!, get yours here:
Engineer’s Log Book PDF download
What are your thoughts? Have I covered everything or is there more you know and would like to share?
I’m always learning and improving this site and my blogs, so please feel free to get in touch with me via LinkedIn or this site to discuss any topics I have covered.
If you’re having trouble finding ways to progress check out this site filled with free learning tools: