The Triumph of Continuous Improvement: Revolutionizing Workflows
Many eyes make bugs shallow – Complex systems
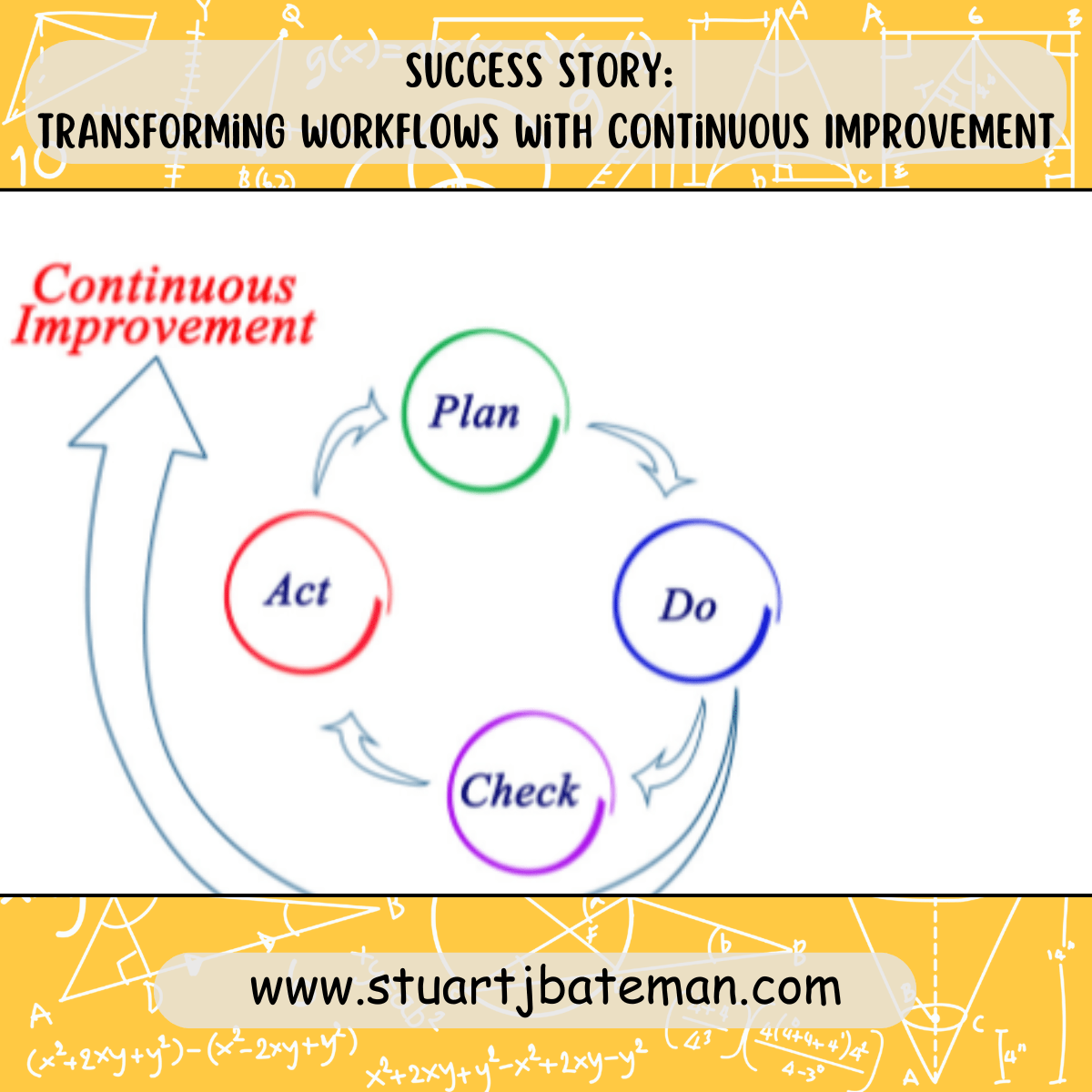
The successful implementation of Continuous Improvement:
This is one of my favourite stories of successful implementation of continuous improvement activities, first I have mentioned before that I implemented an hour long CI session each week, based on the system that I experienced in a previous employer.
At the CI session, I would update the operators as to what I was working on and what was in the pipeline to improve the overall throughput and workplace, after which I opened the floor by asking “What bugs you the most about the production process in this department?”
Now, you could argue I danced with some very dubious dice rolls on this (later I did set more on an agenda to discuss), but these were early days in the change process so there was lots of simple low hanging fruit to grab and have.
Some of the suggestions that came back during one of our sessions was that the current method of transporting our product around the shop floor was open to issues;
- The trollies use were narrow and made from steel angle bars
- There was a weight issue if you didn’t balance these trollies correctly
- The exposed steel bars required constant coverings (in the form of pipe isolation) to protect the product and this needed to be replaced every 2-3 months
- There was a total of about 8 trollies that didn’t meet the demands for the operators (the need was for 10 off)
- The area that was available for the product to sit on, meant that about 50% of it over hanged and could easily be knocked off.
- They were only used for transporting the assembly, so the utilisation of the design was low.
- Many of them were leftovers from the other processes, so I guess it was the case of grab what you could at the time.
The Design
With these issues in mind, I decided to play this opportunity slightly different by getting the operators involved more, this meant that I challenged them to design their ideal trolly. Which I would then cost up and justify the costs for replacing the current setup.
Honestly, this was very enjoyable from start to finish, as I had several designs with ideals to review. The final design blended a few of these ideas (and why not, those ideas were excellent and it helped with the buy in).
This involved a wide frame trolley with box section for the frame and 3 shelves, all with 18mm thick ply and 2 shelves had a simple form design (basically a saw tooth triangle design) which allowed the product to be placed on its side so that other processes that needed to see the numbers could visually see them without moving anything (my training paid off on that idea!). All of which sat on the wheelie bin type wheels and handles for easy control.
Prototype Continuous Improvement
So, we built a prototype and we painted it ourselves, it was so successful we managed to get the other 9 Off and the foam design was even used in several other CI project to eliminate potential damage to parts.
Now, when there are suppliers or customers visiting, managers and myself take the time to point out these trollies to demonstrate to others of what can be achieve, and since this was one of our first wins the operators took onboard the lessons and it never stopped, every day I get stopped by them with a new idea or request or asked for help with waste management, it has been a great start to the lean journey.
Why is this story so important that I use it to demonstrates the power of lean thinking?
- It empowers the operators to own their workplace
- They develop the training given to them in a practical example
- Quick wins can be shown to other departments and roll out the culture of lean thinking
- It shows any idea will improve not just the big ones, I prefer the example of 100 small steps between each large one, the small ones just add up to the same savings and without them those big changes may never take.
- Lean is practice at the end of the day, if you know how to see waste in the system, then you can attack the low hanging fruit without having to study anything. A lot of the time the waste is simple to see, you just need to be trained to attack it.
- It does help having an alliance of people who have experience lean to help get the message across.
This was one of my experiences of CI, I might just describe one of my failures as well to show how that led to another successful solution, but I hope this has shown how easy it is to start and develop a CI culture. How has your CI gone? Please share and discuss with me in the comments.
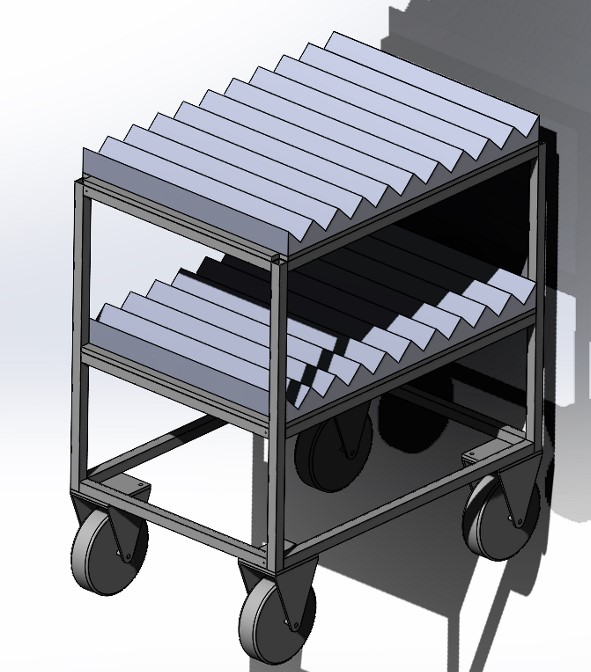
Five key takeaway points:
- Operator Empowerment and Involvement: The blog post highlights how involving operators in the continuous improvement process empowered them to take ownership of their workplace. By encouraging them to design an ideal trolley, I was able to tap into their expertise and insights, resulting in practical solutions that addressed their needs.
- Practical Application of Training: The post discusses how the training provided to operators was put into practical use. The design of the trolley, incorporating a saw tooth triangle design to showcase numbers, exemplifies the effective application of training concepts to solve real-world problems.
- Quick Wins and Culture Propagation: The blog underscores the importance of quick wins in driving the adoption of lean thinking across departments. The success story of the trolley design served as a tangible example that other departments could learn from, fostering a culture of continuous improvement throughout the organization.
- Importance of Small Steps: The post emphasizes the cumulative impact of small improvements. It highlights that while significant changes are important, a series of smaller steps can add up to substantial savings and improvements. This perspective encourages a focus on both major transformations and incremental enhancements.
- Lean Thinking’s Practical Nature: The blog post underscores the practical nature of lean thinking. It suggests that recognizing and addressing waste in processes doesn’t always require exhaustive study. Instead, with proper training, waste can be identified and tackled through simple yet effective measures, making continuous improvement accessible to everyone.
Thoughts
These key points collectively demonstrate the power of involving employees, embracing practical training, leveraging quick wins, valuing small improvements, and emphasizing the practicality of lean thinking in driving successful continuous improvement initiatives.
The books in this piece are some of the many I have read to enrich and develop myself, check out my current reading list and recommendations at:
Or perhaps you would like to learn more? then I recommend my resources page:
There’s also my Engineer’s Log Book PDF download for £1.99!, get yours here:
Engineer’s Log Book PDF download
What are your thoughts? Have I covered everything or is there more you know and would like to share?
I’m always learning and improving this site and my blogs, so please feel free to get in touch with me via LinkedIn or this site to discuss any topics I have covered.
If you’re having trouble finding ways to progress check out this site filled with free learning tools: