15 ways I have implemented to improve a Supply chain
People can only be successful at change if they focus their efforts in a few areas. We recommend a maximum of three areas of improvement at any one time – John H.Zenger
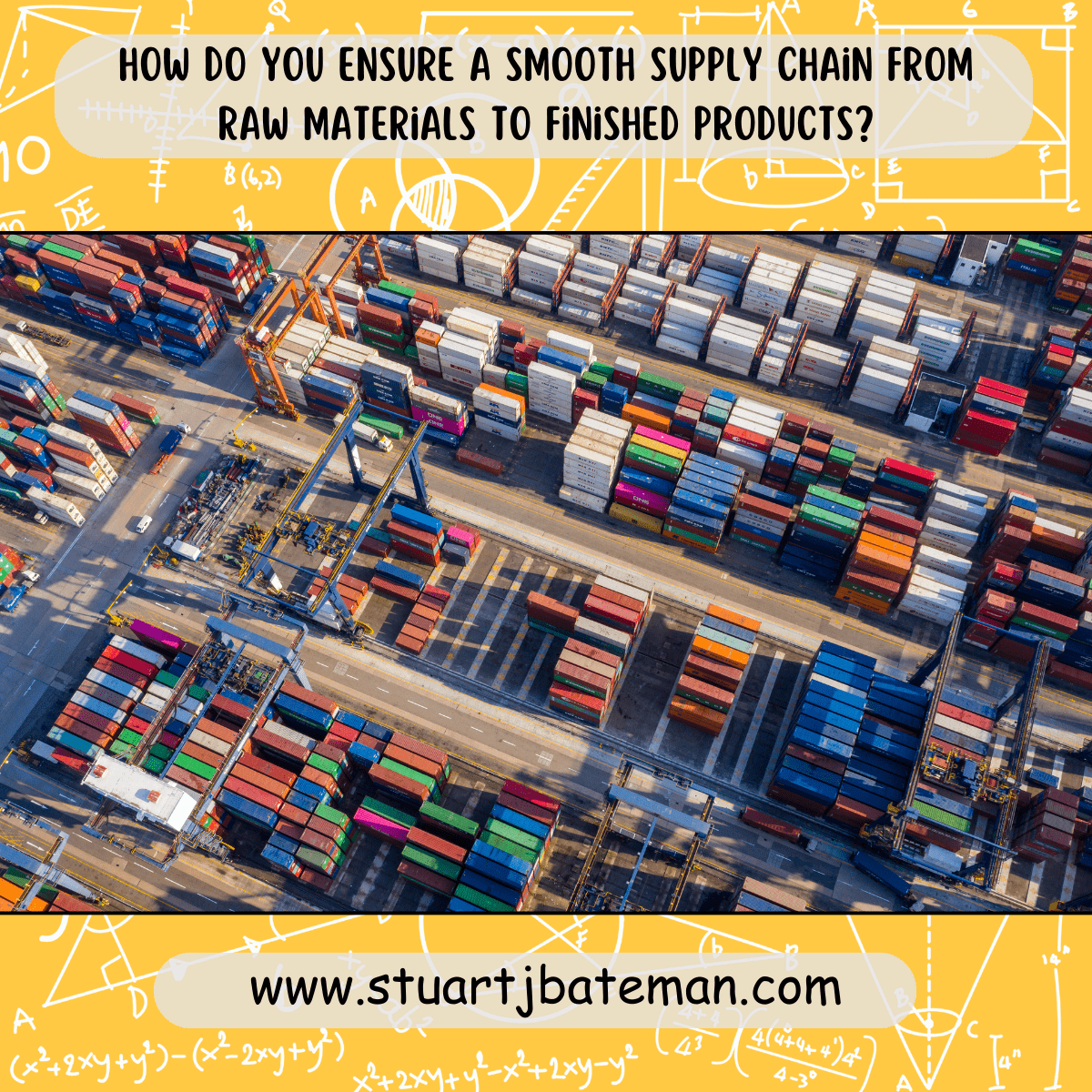
Supply chain headaches
One of the biggest problems in manufacturing is its supply chain, any faults/defects/reworks/random acts of weather or decisions outside your control will have an effect on your product throughput.
Production/Industrial engineers have the responsibility to review and refine the supply chain for companies (mainly internal, but I myself have worked with suppliers), so what can you do?
Methods you can use to smooth flow (no particular order)
1, Ensuring the Raw Material Coming into the System is to Specification:
- Explanation:
- Establishing a robust supplier quality assurance process is essential. This includes defining clear specifications for raw materials, conducting regular audits of suppliers, and implementing incoming material inspection protocols.
- Utilizing advanced tools like Statistical Process Control (SPC) can help monitor material consistency and catch any deviations early.
- Expansion:
- Consider integrating a supplier scorecard system to track and evaluate supplier performance over time. This not only ensures compliance with specifications but also fosters a collaborative relationship with suppliers, driving continuous improvement.
2, Ensuring Parts Flow Smoothly from One Process to Another:
- Explanation:
- Efficient part flow relies on well-designed workflows and process synchronization.
- Implementing Lean principles, such as Value Stream Mapping (VSM), can help identify bottlenecks and streamline processes.
- Expansion:
- Incorporating Just-In-Time (JIT) principles can minimize work-in-progress (WIP) inventory and reduce lead times.
- Automated tracking systems, like RFID or barcoding, can provide real-time visibility into part movement, further ensuring smooth transitions.
3. Ensuring Post-Processing Treatments Conform to Requirements:
- Explanation:
- Post-processing treatments, such as heat treatment or surface finishing, must meet stringent quality standards.
- This requires detailed process documentation, regular calibration of equipment, and routine inspections.
- Expansion:
- Implementing Process Failure Mode and Effects Analysis (PFMEA) can help anticipate potential issues in post-processing and put in place preventive measures.
- Additionally, study the returned parts to measure the surface treatment and work with the supplier to establish the expected levels, then work this into your drawings and control plans.
4. Ensuring Bought-Out Parts Conform to Specifications:
- Explanation:
- Bought-out parts from external suppliers must meet the same rigorous standards as in-house manufactured parts.
- Supplier validation, first-article inspection, and regular audits are key to ensuring conformity.
- Expansion:
- Develop a robust Supplier Quality Management (SQM) system that includes clear contracts specifying quality expectations, and incentivize suppliers for consistent performance.
- Implementing an Approved Vendor List (AVL) can streamline the procurement process and ensure reliable part quality.
5. Ensuring Manufactured Parts Conform to Specifications:
- Explanation:
- In-house manufacturing processes must be tightly controlled to ensure parts meet design specifications.
- This involves setting up standardised work procedures, performing in-process inspections, and using statistical quality control methods.
- Expansion:
- Adopt Six Sigma methodologies to reduce variability and defects in manufacturing processes.
- Establishing a culture of continuous improvement, where operators are encouraged to identify and highlight quality issues, can significantly enhance part conformity.
6. Keeping Machines Serviced and Running (Preventing Breakdowns):
- Explanation:
- Regular maintenance is crucial to avoid unplanned downtime and ensure consistent production.
- Implementing a preventive maintenance (PM) program can help keep machines in optimal condition.
- Expansion:
- Consider moving towards a predictive maintenance (PdM) approach, leveraging data analytics and IoT sensors to predict and prevent equipment failures before they occur. This can significantly reduce machine downtime and increase overall efficiency.
7. Making Sure Information Supplied to Each Department is Correct and Updated Regularly:
- Explanation:
- Accurate and timely information is vital for coordinated decision-making across departments.
- Establishing a centralized communication system, such as an ERP (Enterprise Resource Planning) system, can ensure that everyone has access to up-to-date information.
- Expansion:
- Regular training on data management and the importance of information accuracy should be provided to all employees.
- Additionally, setting up automated data updates and alerts can help maintain the integrity of information flow.
8. Drawing Up Guidelines for Managers/Supervisors and Staff to Follow When Making Decisions:
- Explanation:
- Clear guidelines and standard operating procedures (SOPs) empower staff to make informed decisions that align with company goals.
- These should be documented, easily accessible, and regularly reviewed.
- Expansion:
- Involve employees at all levels in the development of these guidelines to ensure they are practical and applicable.
- Conduct regular workshops to reinforce these guidelines and encourage a culture of shared responsibility in decision-making.
9. Ensuring There is No Demand Inflation:
- Explanation:
- Demand inflation occurs when demand signals are exaggerated, leading to overproduction or stockpiling.
- Accurate demand forecasting, using tools like demand planning software, is essential to prevent this.
- Expansion:
- Implement Sales and Operations Planning (S&OP) processes to align demand forecasts with production capabilities.
- Engage in regular cross-functional meetings to ensure all departments have a clear and realistic understanding of demand.
10. Reducing/Eliminating Scrap:
- Explanation:
- Scrap reduction is critical to improving yield and reducing costs.
- This can be achieved through process optimization, quality control, and root cause analysis of scrap causes.
- Expansion:
- Utilize Lean tools such as Kaizen events and 5S to identify and eliminate waste in the production process. Additionally, adopting advanced manufacturing techniques like additive manufacturing can reduce material waste significantly.
11. Working to Reduce Waste from the System:
- Explanation:
- Waste reduction is a core principle of Lean manufacturing.
- It involves eliminating non-value-added activities, reducing excess inventory, and minimizing downtime.
- Expansion:
- Conduct regular Gemba walks to observe processes firsthand and identify waste.
- Follow up on problem highlighted via Continuous Improvement sessions with the staff to build trust and expand the reach of the system.
12. Ensuring Staff are Trained (Including Cross-Functional Training) to Increase Resource Flexibility:
- Explanation:
- Cross-functional training ensures that employees can perform multiple roles, increasing flexibility and resilience in the supply chain.
- It also helps in filling gaps during peak times or staff shortages.
- Expansion:
- Develop a structured training program that includes both technical skills and soft skills.
- Encouraging a culture of continuous learning and providing opportunities for employees to gain certifications or advanced training can enhance overall workforce capability.
13. Ensuring Staff (Directs and In-directs) are Aware They are Responsible for Quality:
- Explanation:
- Quality is everyone’s responsibility, not just the quality control departments.
- This requires fostering a quality-centric culture where every employee feels accountable for the quality of their work.
- Expansion:
- Implement regular quality awareness programs and integrate quality metrics into employee performance evaluations.
- Recognizing and rewarding employees who demonstrate a strong commitment to quality can reinforce this responsibility.
14. Reducing Variation in Products, Complexity in Design, and Processes to Eliminate Mistakes:
- Explanation:
- Simplifying designs and standardizing processes can reduce the likelihood of errors and defects.
- Design for Manufacturing (DFM) principles and process standardization are key strategies.
- Expansion:
- Encouraging collaboration between design and manufacturing teams early in the product development process can also help in minimizing complexity and potential for mistakes.
15. Continuously Training Everyone to Improve Their Processes, Empowering Them to Look for Quick Wins, and Supporting Their Ideas:
- Explanation:
- Continuous improvement requires ongoing training and empowerment of employees to identify and implement small, incremental changes (quick wins) that can have a significant impact.
- Expansion:
- Establish a formal continuous improvement program, such as a suggestion system or Kaizen board, where employees can share their ideas.
- Provide the necessary resources and support to implement these ideas, and celebrate successes to encourage ongoing participation.
When working on improving the entire supply chain remember
These methods are tops of the trees descriptions of the actual work that’s required to enable flow in the manufacturing supply chain.
The key here is to get the quick wins in first to establish support from departments/operators and suppliers, who will take over running the supply chain once it’s improved (while also continuously improving it).
The books in this piece are some of the many I have read to enrich and develop myself, check out my current reading list and recommendations at:
Or perhaps you would like to learn more? then I recommend my resources page:
There’s also my Engineer’s Log Book PDF download for £1.99!, get yours here:
Engineer’s Log Book PDF download
What are your thoughts? Have I covered everything or is there more you know and would like to share?
I’m always learning and improving this site and my blogs, so please feel free to get in touch with me via LinkedIn or this site to discuss any topics I have covered.
If you’re having trouble finding ways to progress check out this site filled with free learning tools: