5 invaluable tips for dealing with Process variation, dive into unlocking the secrets.
The idea is to make it as easy as possible in the moment to do things that payoff in the long run.- Atomic habits
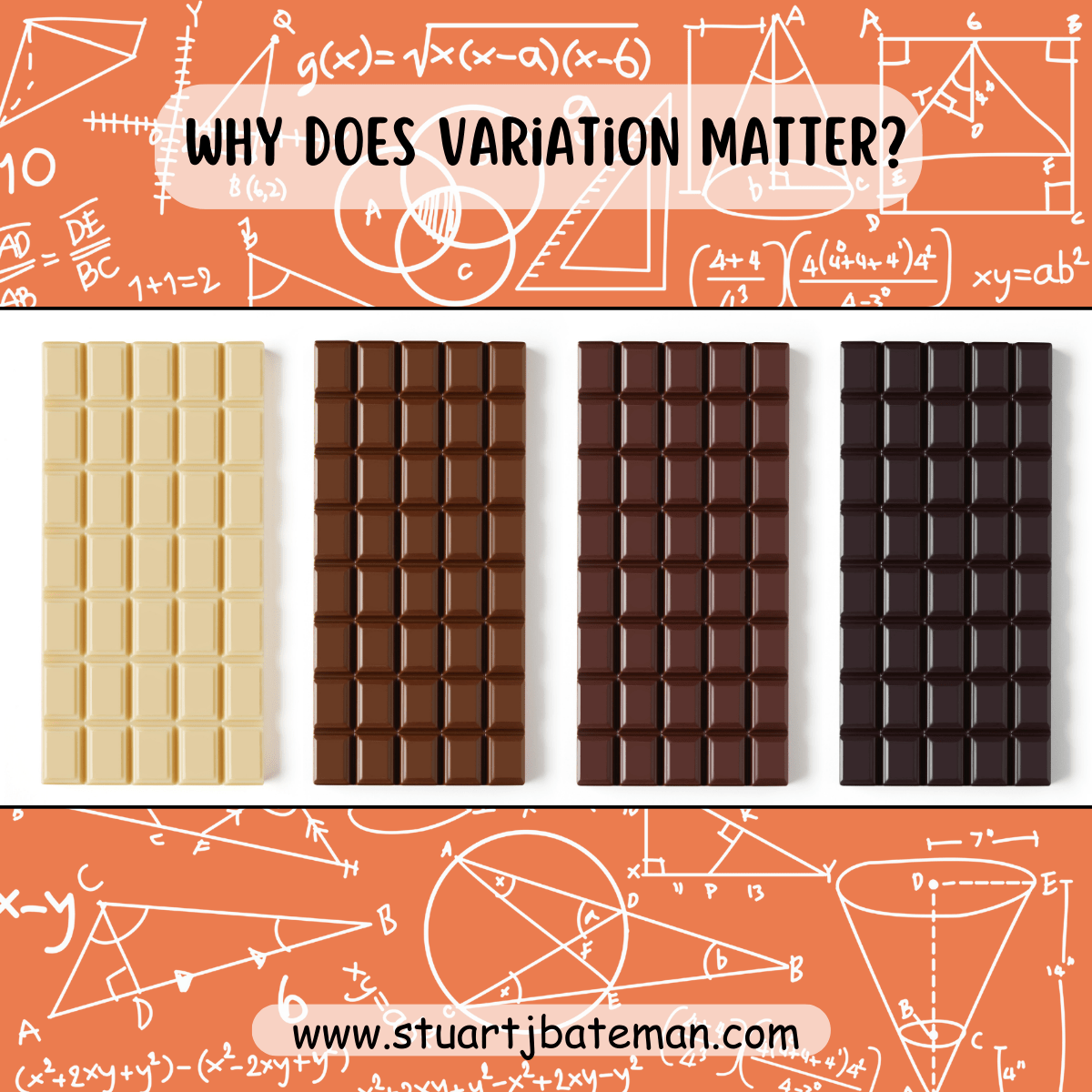
What is Process Variation?
The concept of process variation in manufacturing and services is crucial for understanding its impact on companies.
Process variation is an inherent part of life and is implicitly connected to quantum mechanics.
In manufacturing and other industries, complete elimination of process variation is impossible. Instead, the goal is to minimize its effects on production, whether by improving the process itself, enhancing supporting systems, or providing clear instructions to individuals involved.
Continuous improvement plays a vital role in managing process variation. It involves regularly reviewing processes, monitoring their outputs against desired throughput, and seeking ways to make them more efficient.
To measure and manage variation, various methods are employed, including Statistical Process Control (SPC), Control Charts, Capability Analysis, Measurement System Analysis (MSA), Gage R&R, Design of Experiments (DOE), process auditing, real-time sensors in machines, and inspection.
Process variation can be categorized into two main types: Common Cause Variation and Special Cause Variation.
- Common Cause Variation:
- Â Common Cause Variation is the natural output variation that arises from any process. It is often depicted as the random fluctuations within the bell curve of a histogram, following a normal distribution.
- As long as this variation falls within the specified limits, there is no immediate cause for concern. It is considered inherent and manageable.
- In the context of probability, if we aim for the nominal dimension (mean) 99% of the time, our components and assemblies will function optimally.
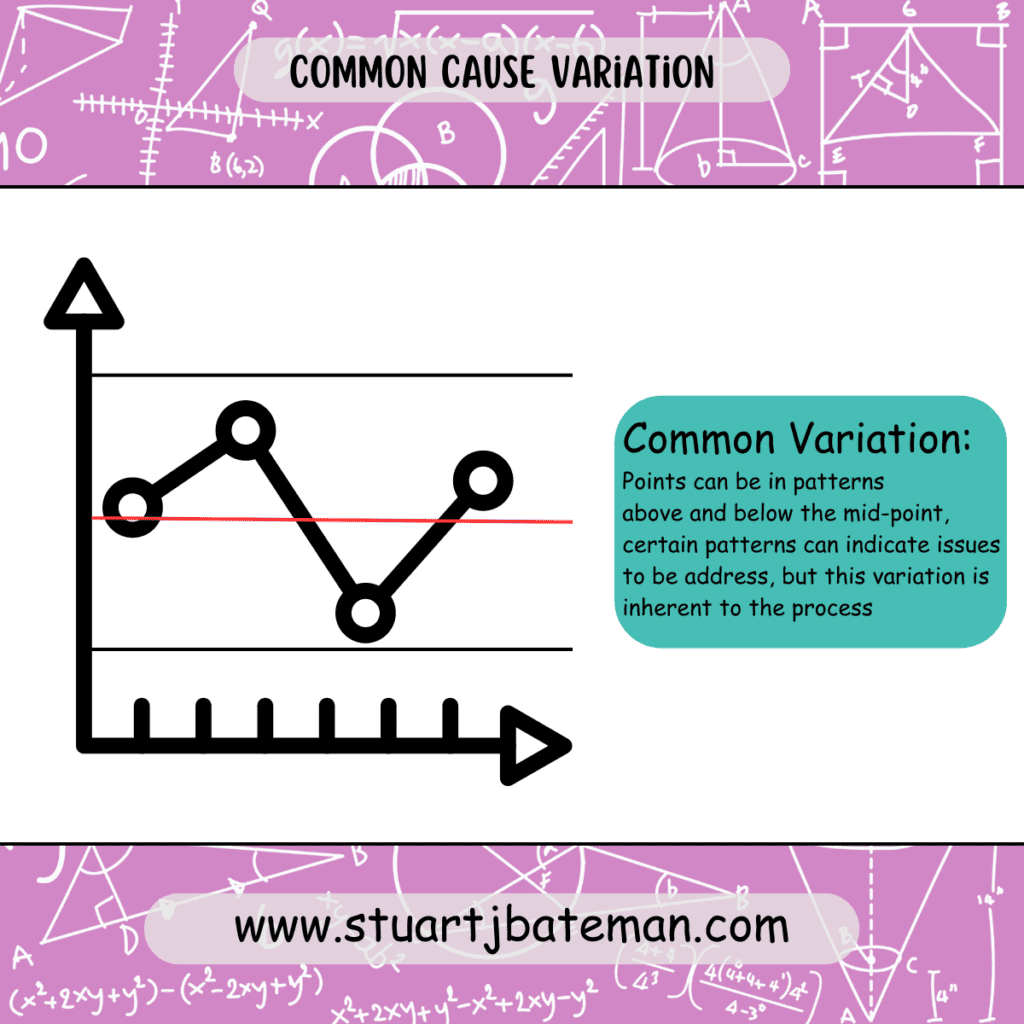
- Special Cause Variation:
- Special Cause Variation, on the other hand, is caused by external factors that the process cannot control. These factors are often outliers in the bell curve.
- These causes can be related to man, machine, method, measurement, or environment, among others. Identifying and addressing them is crucial for problem-solving and quality improvement.
- Techniques like Ishikawa diagrams can be used to trace the root cause of special cause variation.
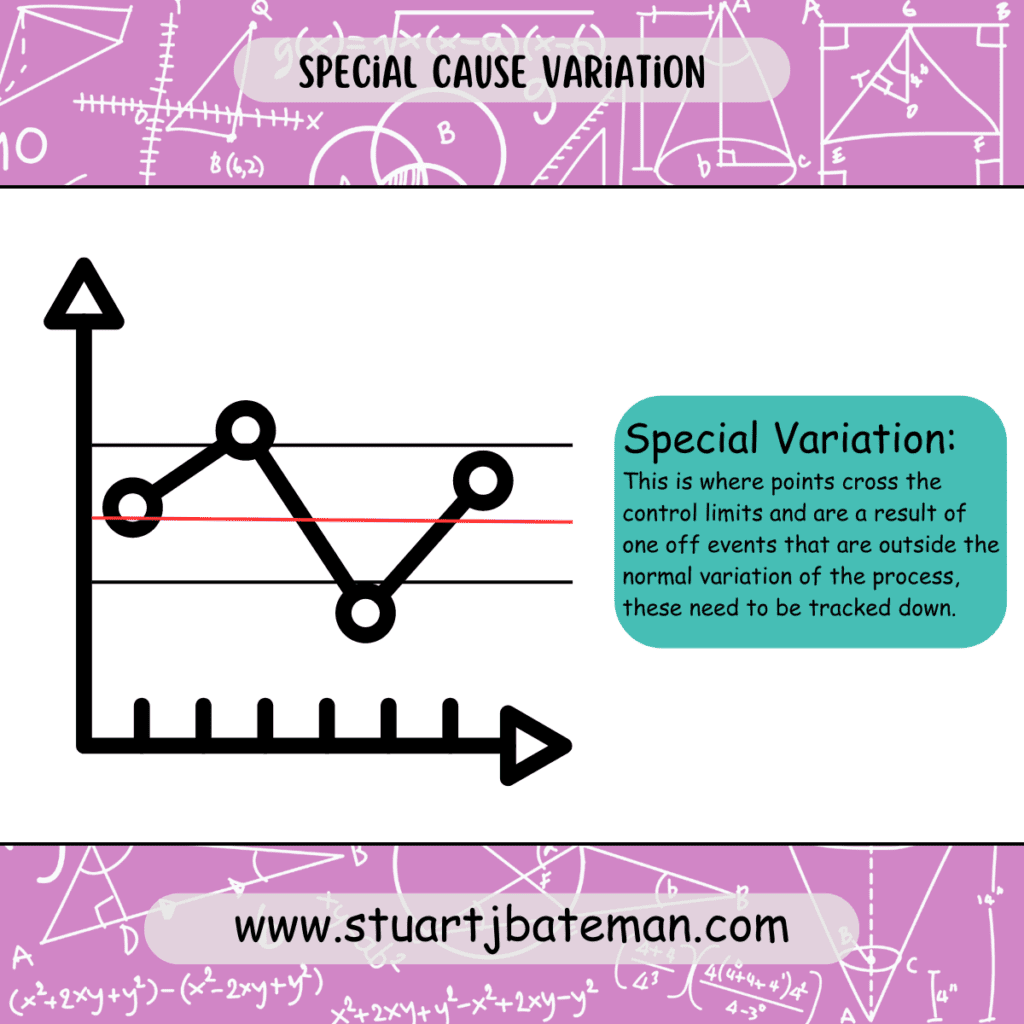
Deming’s philosophy emphasizes that improving processes is the path to achieving quality. Even though some level of random variation is inevitable, the goal is to be as close to the nominal dimension as possible for consistent and efficient operations.
Understanding the Bell Curve and Probability:
- The bell curve, representing normal distribution, helps visualize the frequency of measurements falling within specific bins or ranges.
- To reduce random variation, the objective is to make the frequency bar over the mean more common, essentially narrowing the curve.
- For special cause variation, frequent points outside the limits can shift the mean, indicating a need for investigation.
In general, reducing random variation is a challenging and expensive endeavour compared to addressing the root causes of special cause variation. One important metric used in this context is CPK, which assesses process capability. A CPK ratio of 1.33 or higher is considered capable, indicating that the process can consistently meet specifications.
Beyond manufacturing, the concept of variation extends to various business processes. While complete elimination of variation is often impossible, managing it through continuous improvement methodologies like Statistical Process Control (SPC), Control Charts, and other techniques is crucial. This ongoing effort ensures that processes remain efficient and product quality is consistently maintained.
Furthermore, recognizing the connection between variation and its impact, as well as employing various measurement and management methods, is vital for businesses striving for excellence and customer satisfaction. By minimizing variation, companies can enhance their competitiveness and ensure consistent product quality that meets customer expectations.
Here are five practical tips for managing and addressing variation in manufacturing and business processes:
- Differentiate Between Common and Special Cause Variation:
- Understand that not all variation is equal. Distinguish between common cause (random) and special cause (assignable) variation. Common cause variation is inherent and should be managed within specified limits, while special cause variation requires investigation and problem-solving.
- Implement Statistical Process Control (SPC):
- Utilize SPC tools and Control Charts to monitor and control variation. These tools provide real-time insights into process stability and help identify when special cause variation occurs. Regularly reviewing control charts can prevent potential issues from escalating.
- Conduct Root Cause Analysis:
- When special cause variation is detected, conduct a thorough root cause analysis to identify the underlying factors contributing to the problem. This may involve using tools like Ishikawa diagrams or the 5 Whys technique to trace the causes.
- Embrace Continuous Improvement:
- Adopt a culture of continuous improvement, as advocated by Deming. Regularly review and improve processes to reduce random variation and address the root causes of special cause variation. Encourage employees to contribute their insights and ideas for improvement.
- Monitor Process Capability (CPK):
- Keep a close eye on process capability using metrics like CPK. A CPK ratio of 1.33 or higher indicates that the process is capable of consistently meeting specifications. If the CPK falls below this threshold, prioritize process improvement efforts.
By following these tips, you can effectively manage variation, enhance process efficiency, maintain product quality, and ultimately meet customer expectations.
Conclusion:
Effectively managing variation is crucial for achieving consistent product quality and process efficiency. By differentiating between common and special cause variation, implementing SPC, conducting root cause analysis, embracing continuous improvement, and monitoring process capability, businesses can enhance their competitiveness and meet customer expectations.
Are you ready to take control of variation in your processes? Start implementing these tips today and drive your business towards excellence in quality and efficiency!
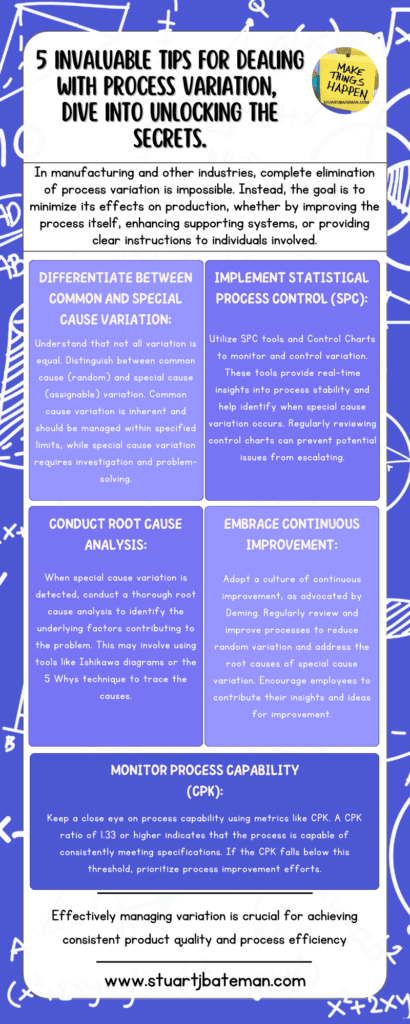
The books in this piece are some of the many I have read to enrich and develop myself, check out my current reading list and recommendations at:
Or perhaps you would like to learn more? then I recommend my resources page:
There’s also my Engineer’s Log Book PDF download for £1.99!, get yours here:
Engineer’s Log Book PDF download
What are your thoughts? Have I covered everything or is there more you know and would like to share?
I’m always learning and improving this site and my blogs, so please feel free to get in touch with me via LinkedIn or this site to discuss any topics I have covered.
If you’re having trouble finding ways to progress check out this site filled with free learning tools: