3S Methodology Guide: Sort, Set, Shine for Lean Manufacturing
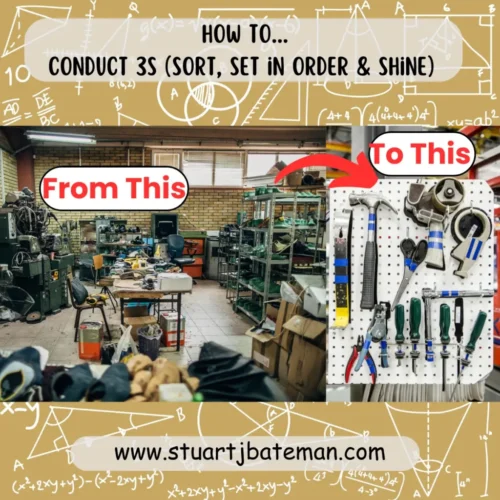
Wisdom is given equally to everybody, the point is whether one can exercise it. – Taiichi Ohno
What is 3S Methodology? Complete Definition
The 3S methodology is a lean manufacturing approach that transforms workplace organization through three systematic steps: Sort, Set, and Shine. Unlike the full 5S system, 3S methodology delivers 90% of organizational benefits with simplified implementation, making it perfect for teams new to lean manufacturing.
Quick 3S Overview:
- Sort: Remove unnecessary items and clutter
- Set: Organize remaining items logically by usage frequency
- Shine: Clean and inspect workspace regularly
The 3S methodology originated from Toyota’s 5S system but focuses on the three foundational elements that provide the most immediate impact for workplace productivity and safety.
Table of Contents
- 3S vs 5S Methodology: Which Approach is Right for You?
- Step 1: Sort – Removing Unnecessary Items from Your Workspace
- Step 2: Set – Organizing Tools and Materials by Usage Frequency
- Step 3: Shine – Maintaining Clean, Productive Work Environment
- 3S Methodology Implementation: Complete Step-by-Step Guide
- 3S Lean Manufacturing Benefits and ROI Analysis
- When to Use 3S Methodology vs Full 5S Implementation
- 3S Implementation Success Tips from Real Experience
- Conclusion: Strategic 3S Methodology Implementation
- Frequently Asked Questions About 3S Methodology
3S vs 5S Methodology: Which Approach is Right for You?
Before diving into 3S methodology implementation, let’s understand how it compares to the traditional 5S workplace organization system.
5S Background: The 5S system has been around for over 60 years, focusing on workplace organization to minimize downtime from missing tools, equipment, jigs, information, and parts.
5S Methodology Objectives:
- Reduce the 7 wastes of lean manufacturing
- Reduce process variation and improve quality
- Improve productivity through organized workspaces
- Promote workplace stability for continuous improvement
Why Choose 3S Methodology Over 5S?
Based on my experience implementing workplace organization at Lewmar, Stannah, and AI, I’ve found that starting with 3S methodology offers several advantages:
3S delivers 90% of 5S benefits with significantly less complexity. As Paul Akers demonstrates, lean implementation doesn’t have to be difficult – small, consistent steps forward are more sustainable than overwhelming comprehensive programs.
3S Methodology Advantages:
- Faster implementation (2-4 weeks vs 3-6 months)
- Less resistance from workforce
- Immediate visible results
- Natural progression to full 5S when ready
- Easier to sustain long-term
Before we go deeper, check out this informative video from LeanSmarts explaining 5S!
https://www.youtube.com/watch?v=SODLdxMkVAM
Step 1: Sort – Removing Unnecessary Items from Your Workspace
The Sort phase of 3S methodology involves systematically removing items that don’t contribute to daily work efficiency.
Sort Implementation Process:
Equipment needed: Pen, paper, and plenty of red floor tape.
Step-by-step Sort process:
- Remove everything not used daily – Be ruthless. In most companies, especially smaller ones, you’ll find items so old only the original owner knows their purpose.
- Set sorting criteria – Categorize items by usage frequency:
- Daily: Used every workday
- Weekly: Used 1-4 times per week
- Monthly: Used 1-4 times per month
- Annually: Used less than monthly
- Create quarantine area – Move EVERYTHING that isn’t permanently fixed into this designated space. Yes, everything including tools, equipment, documents, (desks, benches, file cabinets, and work-in-progress inventory are optional of course).
- Identify quarantined items – Catalog each item: What is it? How often is it actually used? Who uses it?
- Use Red Tag system – Either purchase red tags or use a permanent marker to label items with identification numbers and usage frequency.
- 6-12 month holding period – Items that can’t be identified or haven’t been used get held in quarantine. Document with drawings/photos before discarding anything.
Sort Decision Framework:
- Daily items: Return to workspace with designated locations
- Weekly/Monthly: Store in department but away from primary work area
- Annual/Unknown: Remove from workspace entirely
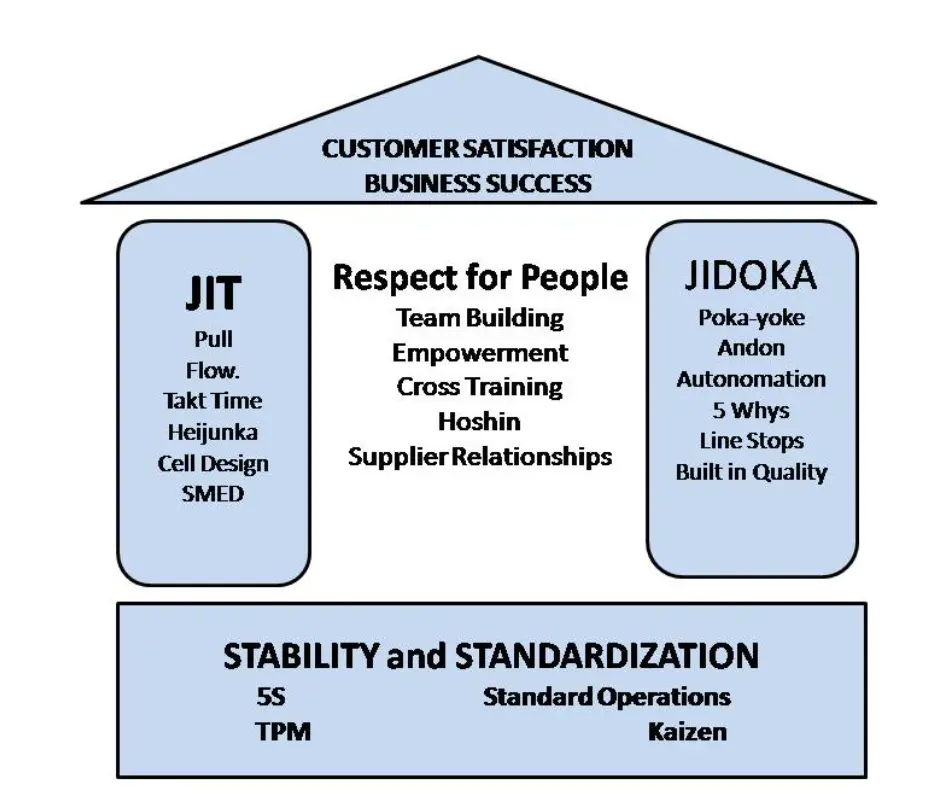
Step 2: Set – Organizing Tools and Materials by Usage Frequency
The Set phase of 3S methodology creates logical organization based on how frequently items are needed in the workflow.
Set in Order Implementation:
Location Strategy by Usage Frequency:
- Daily items: Located directly at the workstation where they’re used
- Weekly items: Nearby rack or locked cupboard within 30 seconds travel time
- Monthly items: Department storage area
- Annual items: Consider elimination rather than storage
Workplace Organisation Principles:
- No sharing of daily tools – If multiple operators need the same tool, buy/make additional copies rather than sharing
- Shadow boards for visual management – Organize tools in order of workflow sequence
- 30-second rule – Keep all regularly used tooling, information, and fixtures within 30 seconds of where they’re needed
- Flow optimization – Arrange tool locations to match the natural workflow sequence
Creating Effective Storage Systems:
When designing shadow boards and tool storage:
- Consider product flow and process sequence
- Arrange tools in order of use
- Make missing tools immediately obvious visually
- Ensure easy access without interference to workflow
This organizational approach supports both Standard Operating Procedures (SOPs) and builds muscle memory so operators immediately notice when something is wrong.
Step 3: Shine – Maintaining Clean, Productive Work Environment
The Shine phase of 3S methodology transforms cleaning from a chore into a detailed inspection system that prevents problems.
Shine as Inspection Strategy
Philosophy: Cleaning is detailed inspection. When we clean tools, boards, benches, and equipment, we get close enough to notice developing problems before they cause downtime.
This principle comes from Total Productive Maintenance (TPM) – just like checking your car twice monthly helps you identify and address issues before they become problems.
Shine Implementation Process:
- Allocate dedicated time – Set aside 10-15 minutes at the end of each shift for cleaning and inspection
- Clean all work areas:
- Desks and office areas
- Machines and production equipment
- Benches and workstations
- Storage areas and tool locations
- Inspection during cleaning:
- Check that everything is present and working
- Verify SOPs are current and accessible
- Identify wear patterns or developing issues
- Note any missing or damaged items
- Document findings – Record any issues discovered during the shine process for follow-up action
Shine Benefits:
- Early problem detection before equipment failure
- Maintained tool accuracy and reliability
- Safe, organized work environment
- Operator ownership and pride in workspace
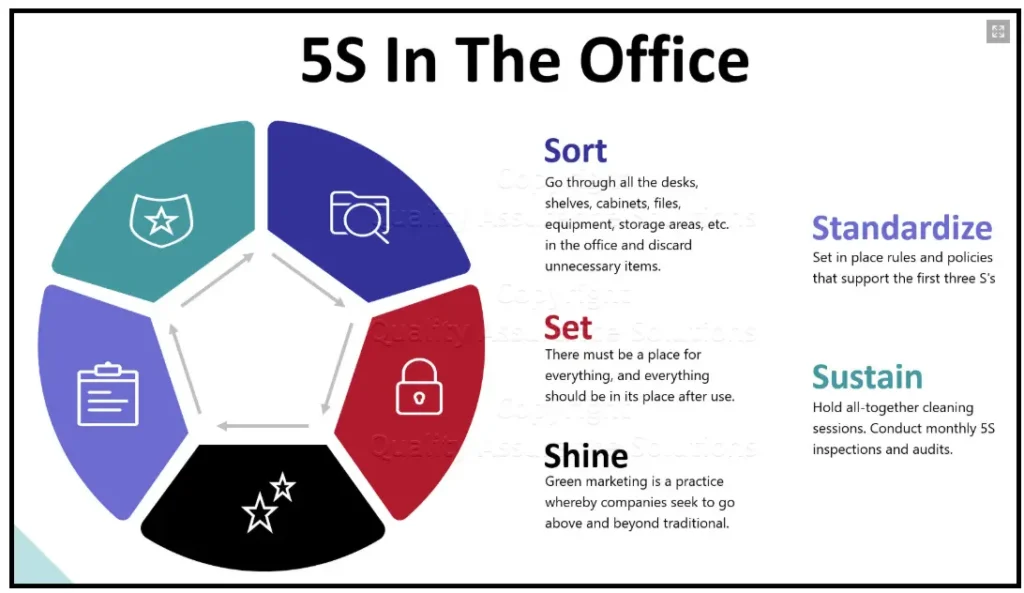
3S Methodology Implementation: Complete Step-by-Step Guide
Based on my experience implementing 3S methodology at Lewmar, Stannah, and AI, here’s the proven implementation approach:
Phase 1: Planning and Preparation (Week 1)
- Select pilot area for initial implementation
- Gather supplies: red tape, tags, cleaning supplies
- Communicate purpose and benefits to team
- Schedule dedicated time for 3S activities
Phase 2: Initial 3S Event (Week 2)
- Conduct Sort phase over 2-3 days
- Implement Set phase organization
- Establish Shine cleaning routines
- Take before/after photos for documentation
Phase 3: Habit Formation (Weeks 3-4)
- Daily 15-minute shine activities
- Weekly review of Sort decisions
- Monthly re-evaluation of Set arrangements
- Track improvements and celebrate wins
Phase 4: Expansion (Month 2+)
- Apply 3S methodology to additional areas
- Train additional team members as 3S facilitators
- Develop standardized procedures for sustainment
3S Lean Manufacturing Benefits and ROI Analysis
The 3S methodology delivers measurable benefits that support broader lean manufacturing objectives:
Immediate 3S Benefits:
- Find anything within 30 seconds – Eliminates time waste searching for tools
- Visual workplace management – Operators find items without guides or reading
- Reduced tool hoarding – Items stay at processes where needed, not in personal toolboxes
- Improved safety – Clean, organized workspaces reduce accidents
- Enhanced training – New workers understand processes faster without clutter
Business Impact Benefits:
- Maximized floor space – Creates room for new production lines
- Standardized work areas – Enables cross-training and flexible staffing
- Preventive maintenance integration – Damaged items identified and replaced immediately
- Document management – SOPs reviewed and updated regularly
- Continuous improvement culture – Regular focus on identifying the 7 wastes
Productivity Improvements:
Conduct time studies before and after 3S implementation to quantify gains. Typical improvements include:
- 15-25% reduction in material handling time
- 10-20% increase in productive work time
- 30-50% reduction in setup/changeover times
- Significant reduction in safety incidents
When to Use 3S Methodology vs Full 5S Implementation
There are two schools of thought on workplace organization timing in lean manufacturing:
Option 1: Start with 3S Methodology (Recommended)
Best for: Teams new to lean, small to medium operations, quick wins needed
Implement 3S methodology at the beginning of lean initiatives as:
- Foundation for other lean tools
- Quick win to build momentum
- Waste elimination before advanced techniques
- Team engagement and buy-in building
Option 2: Full 5S After Process Improvement
Best for: Mature lean operations, comprehensive facility transformation
Implement 5S methodology after:
- Individual station improvements completed
- Team trained on lean principles one-on-one
- Process standardization achieved
- Management systems developed
My Preferred Approach: 3S First
Based on experience, I recommend starting with 3S methodology during continuous improvement sessions. This approach provides:
- Individual training opportunities – Work one-on-one with operators on lean principles
- Positive team feedback – Straightforward activities that show immediate results
- Management visibility – Clean, organized areas impress visitors and leadership
- Natural progression – Easy transition to Standardize and Sustain (the final 2S)
Adding the Final 2S Elements:
Standardize: Document the 3S methodology procedures and create rotation schedules for responsibilities
Sustain: Focus on maintaining the first 3S consistently – the management system comes naturally from regular practice
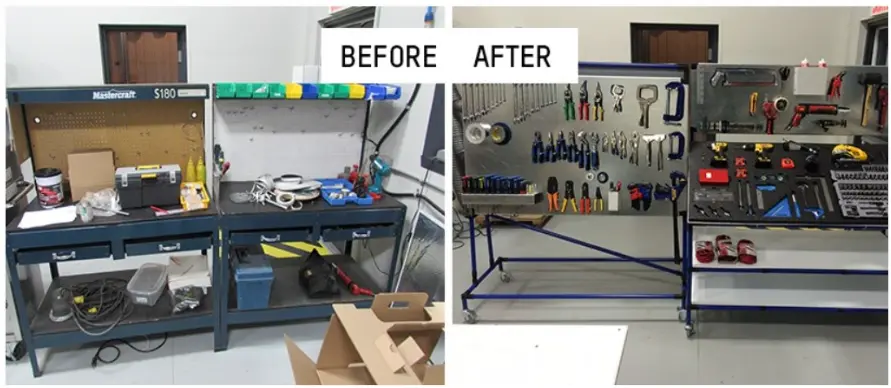
3S Implementation Success Tips from Real Experience
Drawing from Atomic Habits by James Clear, successful 3S methodology implementation follows proven habit formation principles:
Creating Good 3S Habits:
- Make it obvious: Visual cues and clear procedures
- Make it attractive: Celebrate improvements and recognize participation
- Make it easy: Simple, short activities that fit into daily routine
- Make it satisfying: Immediate visible results and team appreciation
Breaking Bad Workplace Habits:
- Make clutter invisible: Remove temptation to accumulate unnecessary items
- Make disorganization unattractive: Highlight costs of inefficiency
- Make poor practices difficult: Design systems that promote organization
- Make mess unsatisfying: Connect disorder to productivity problems
3S Methodology Questions for Success:
When implementing workplace organization changes, ask:
- How can we make organization obvious?
- How can we make cleaning attractive?
- How can we make good practices easy?
- How can we make improvements satisfying?
Conclusion: Strategic 3S Methodology Implementation
The 3S methodology isn’t just about cleaning – it’s about creating a foundation for operational excellence. As Michel Greif explains in “The Visual Factory,” workplace organization affects the daily environment where operators spend their time. They should have input on organization and take pride in maintaining conditions that benefit everyone.
Key Implementation Success Factors:
- Start small and build momentum with pilot areas
- Train everyone to audit the 3S process for sustainability
- Establish rotation schedules to promote leadership and responsibility
- Focus on habit formation rather than one-time events
- Measure and celebrate improvements to maintain engagement
Ready to Implement 3S Methodology?
By taking a strategic approach and following these proven 3S steps – Sort, Set, and Shine – you can create a clean, productive workplace that serves as the foundation for advanced lean manufacturing techniques.
If you’re ready to start implementing 3S methodology in your organization, consider working with a certified Lean Six Sigma professional to ensure the process delivers maximum results efficiently.
Frequently Asked Questions About 3S Methodology
Q: What’s the difference between 3S methodology and 5S? A: 3S methodology focuses on Sort, Set, and Shine – the three foundational steps that provide 90% of workplace organization benefits. 5S adds Standardize and Sustain, making it more comprehensive but complex to implement initially.
Q: How long does 3S methodology implementation take? A: Most teams see results within 2-4 weeks for individual work areas. The initial 3S event takes 2-3 days, followed by daily 15-minute maintenance activities.
Q: Can 3S methodology work in office environments? A: Absolutely. 3S methodology applies to any workspace where organization impacts productivity – manufacturing, healthcare, offices, warehouses, and service environments.
Q: What’s the ROI of 3S methodology implementation? A: Typical improvements include 15-25% reduction in material handling time, 10-20% increase in productive work time, and 30-50% reduction in setup times. Conduct time studies before and after for specific measurements.
Q: How do you sustain 3S methodology long-term? A: Focus on daily 15-minute shine activities, weekly sort reviews, and monthly set arrangement evaluations. Train multiple team members to audit and lead 3S activities through rotation schedules.
References and Continued Learning
- The Lean Toolbox – Bicheno & Holweg
- The Lean Six Sigma Pocket Toolbox – George, Rowlands, Price & Maxey
- Lean Thinking – Womack and Jones
- The Toyota Way Fieldbook – Liker and Meir
- The Visual Factory – Michel Greif
- Atomic Habits – James Clear
The books in this piece are some of the many I have read to enrich and develop myself, check out my current reading list and recommendations at:
Or perhaps you would like to learn more? then I recommend my resources page:
There’s also my Engineer’s Log Book PDF download for £1.99!, get yours here:
Engineer’s Log Book PDF download
What are your thoughts? Have I covered everything or is there more you know and would like to share?
I’m always learning and improving this site and my blogs, so please feel free to get in touch with me via LinkedIn or this site to discuss any topics I have covered.
If you’re having trouble finding ways to progress check out this site filled with free learning tools: