How to… use Total productive maintenance (TPM)
If you’re having trouble changing your habits, the problem isn’t you. The problem is your system. – Atomic Habits
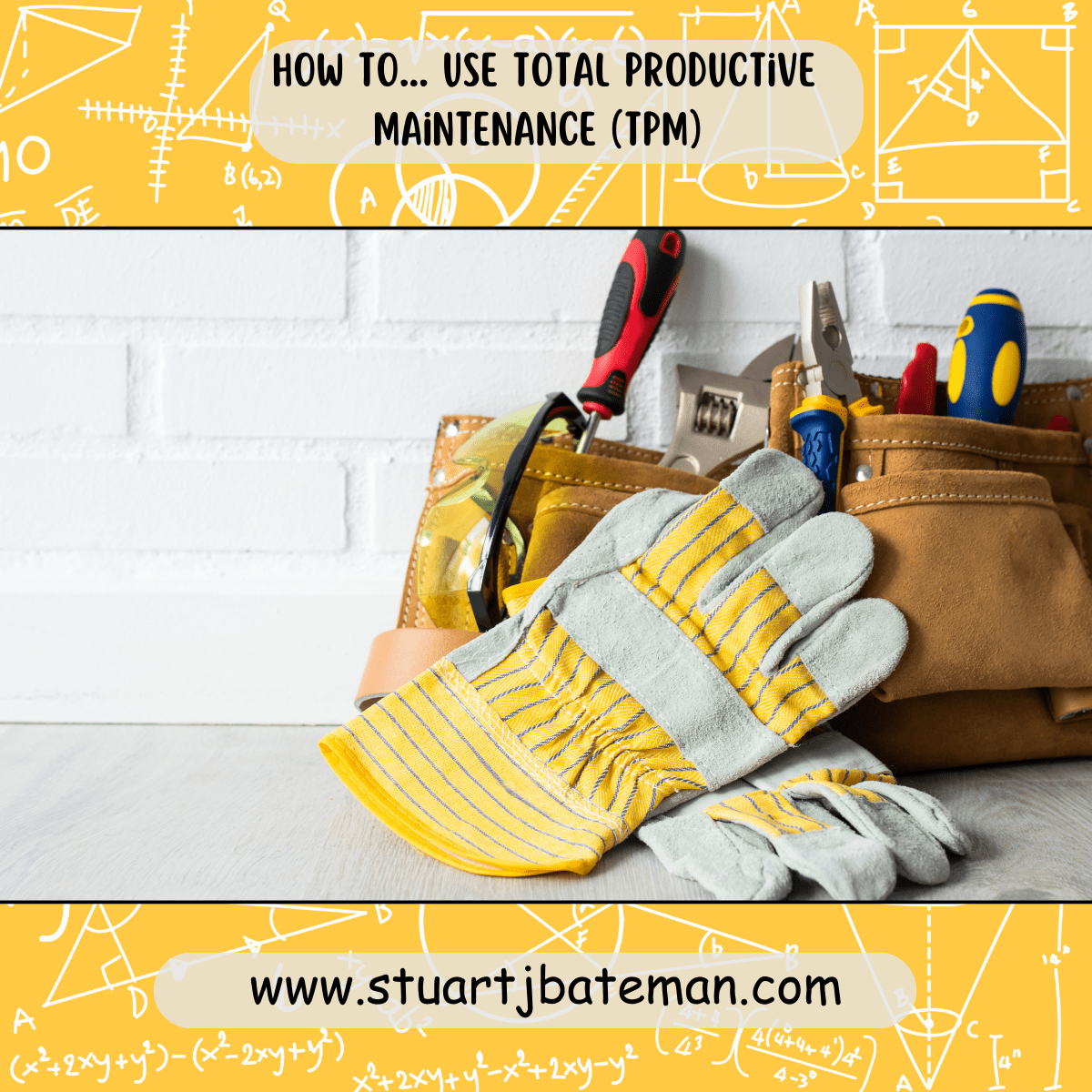
What is Total productive maintenance TPM?
Total productive maintenance is a method used to support and maintain equipment by breaking them into elements, understanding risks to failure and occurrence, repair machines to a accepted standard to maintain via regular inspection and cleaning. If checks identify a fault or non-conformance, this is reported to the process manager to arrange repairs. Common spares to be stocked in-house and working with the machine manufacturer, draw up a timetable of regular maintenance.
Benefits of implementing and running TPM?
Total productive maintenance in a nut shell: you wouldn’t like your car breaking down on you out of the blue on a cold December morning with a fog coming in and rain is likely. Yup, you want to know as soon as possible if there are problems on the horizon, and the earlier you know the more time you have to source the problem / organise the service and parts / spread the cost of the repair and reduce the impact to your day (or in this case your throughput).
Basically, if we think in the simple terms, cost / time and delivery are metrics that many companies used, as well as efficiency of assets and if one goes down, that efficiency goes to 0. Think the point is clear, and in the book ‘The Goal’ a similar term is used by the Professor to generate buy in for the TOC method, if your constraint goes down it’s not the cost per hour of the one machine, it’s the cost per hour of the whole production line.
Steps to implementing TPM (how I did it after reading and researching the method).
Reading the book ‘TPM: the western way’ there are two methods to implement, the first being Total productive maintenance TPM and the second which is more of an in depth method call P-M analysis (we’ll get to that later).
Steps I took:-
1, Review the production line and choose the machine / station you want to focus on (in my case I choose the process constraint because of that saying from the goal).
- Here is a useful tool I have used, as you will see it’s a simple scoring matrix that with the help of the operators (and it should be done with them) you can find the priority machine to start with and in most cases it’ll be the constraint/bottleneck:
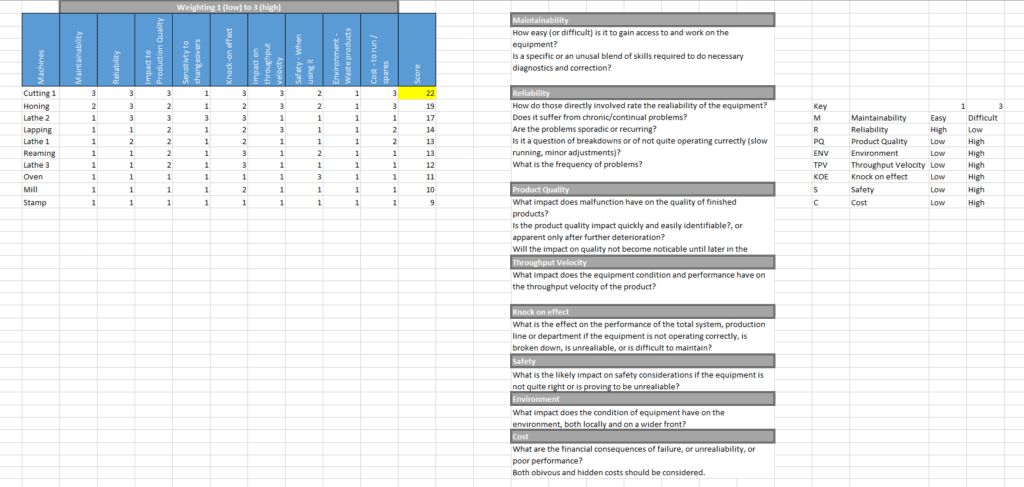
2, Asses the current condition of the machine you want to focus on by breaking the major systems of the machine down into 5-6 sub headings like:
- Mechanical
- Pneumatic
- Hydraulic
- Cutters
- Coolant
- Electrics
- This helps to identify areas of concerns later on
- Here’s the sheet I use to classify toe components under the system above:
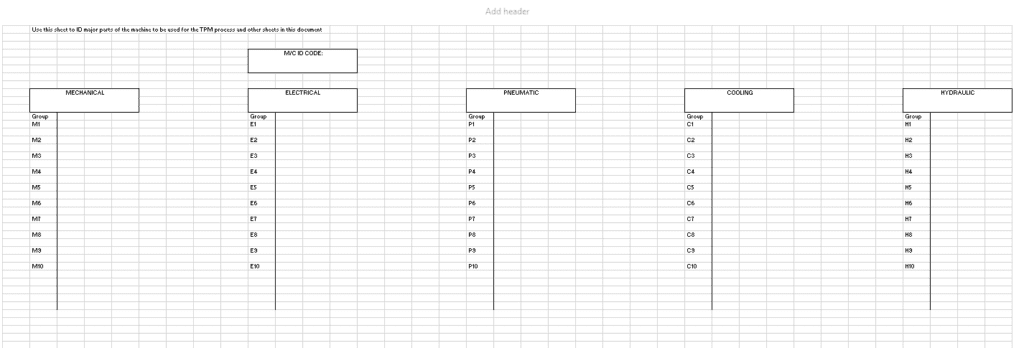
3, Now we conduct the condition appraisal of the focus machine going through the major components we highlighted earlier.
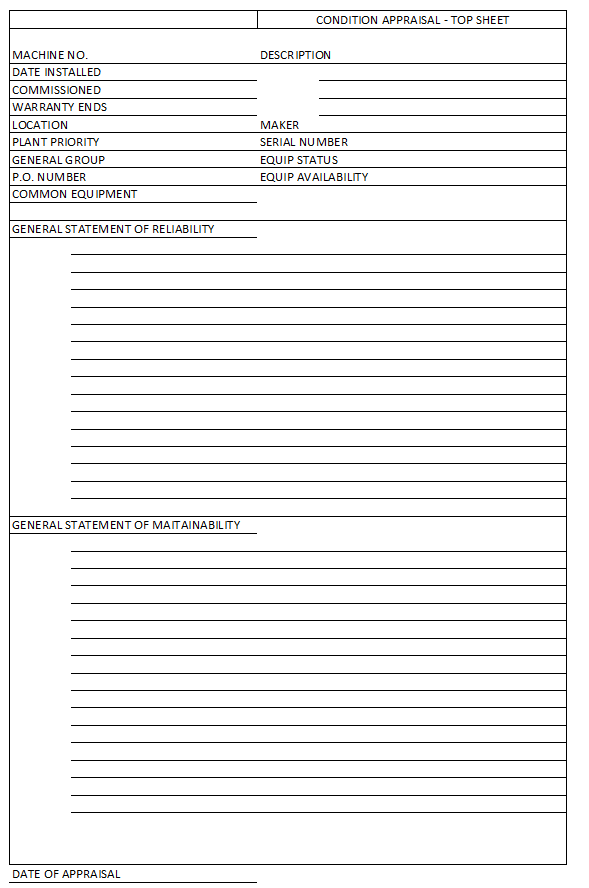
- Again with the help of the operators the first sheet can be filled in, this will be opinion based unless you’re running OEE to monitor machine breakdowns.
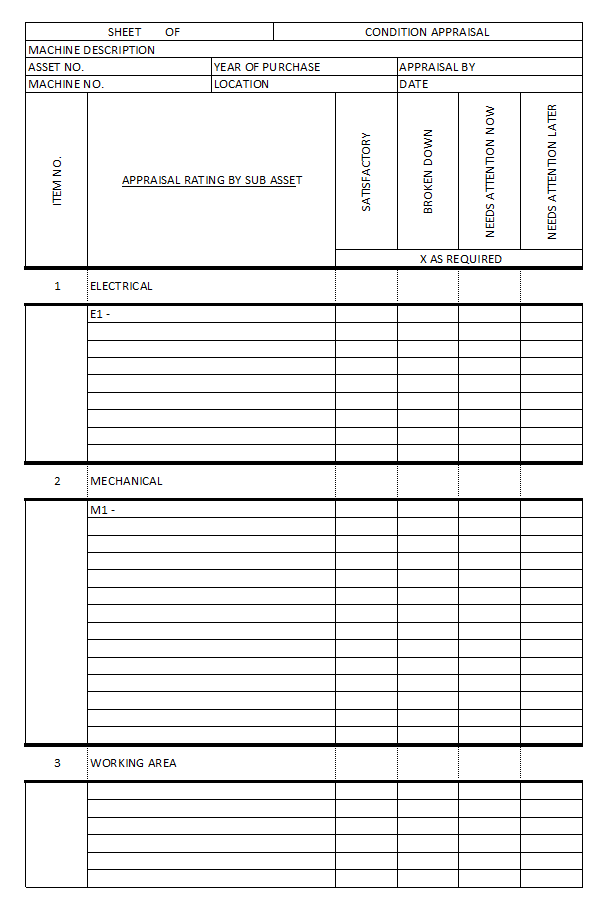
- Using the chart from step 2 appraise each area using these sheets, here we are doing a deep dive into the systems and looking for issues that need to be brought back to a agreed operational condition, put your inspectors hat on and poke around, the section headings allow us to audit the machine.
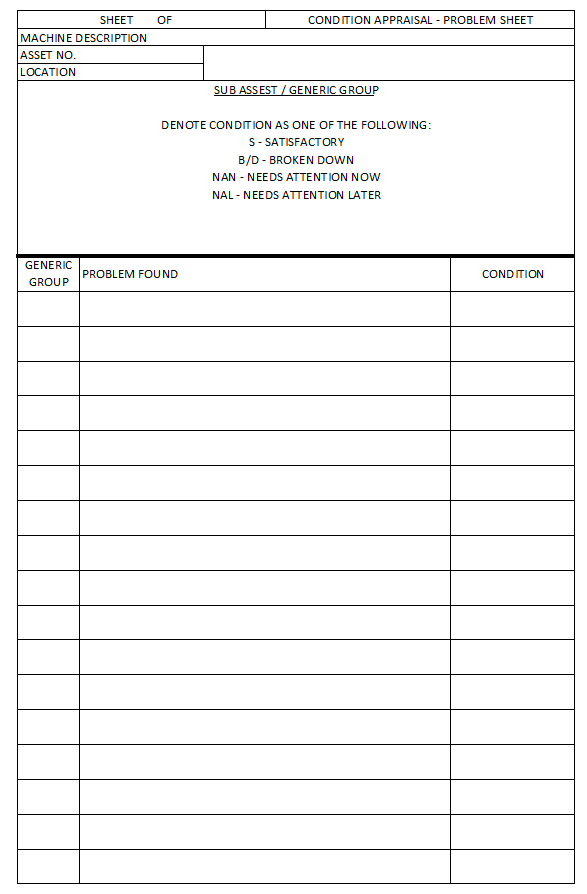
- After the appraisal, this sheet allows us to write down the issues and what group they belong to, this can create the priority work list for a contractor to work to.
4, Once you have the condition list, work with the manufacturer or contractor to bring the machine back to the agree condition to which the workers will watch over.
5, Now, this is when we can do two things
- First we need to draw up a maintenance schedule for routine checks by the operators and what checks / service will be done by the manufacturer or service contractors
- This list needs to be weekly/monthly and annually
- Operators are only tasked to inspect / clean and top up fluids
- Next we need to built a list of known spares and understand if any are critical (long lead times) that we need to have on site.
- Speak to the manufacturer for help, also track the breakdowns and the parts that fail to build up your own list of parts along with the mean time between failures.
6, Once that’s done we need to create the routine for checking, and I’ve found it easy to nominate one person per day to look after the focus machine using a schedule like this one:
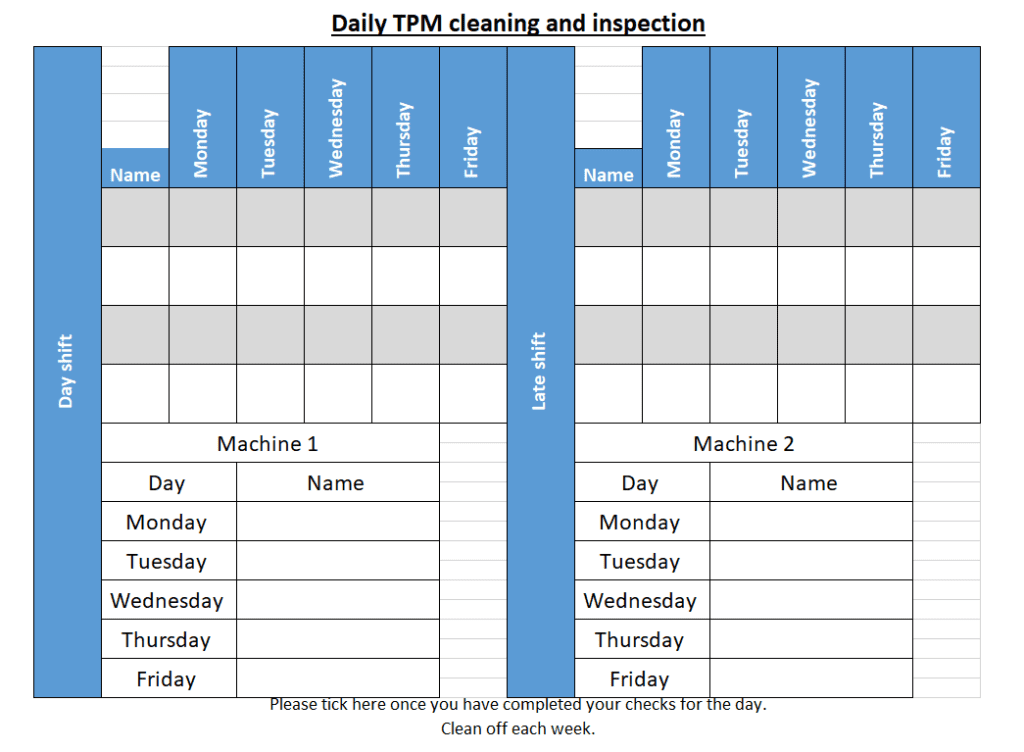
7, That’s the easy part, now the next ties in with OEE where we monitor the machine and understand its Mean time between failure as we want to be proactive in maintenance and not reactive, as it’s better to schedule downtime and make allowances then be surprised and have to spend time / money to make up the lost production.
How I monitor the machines – to see if the daily Total productive maintenance TPM has or is making an impact
It’s not rocket science, I use a tick sheet on each machine that the operators and myself have taken the time to refine into a 2 second job that gives us the maximum details to calculate the metrics required for OEE, and here’s what that sheet looks like:
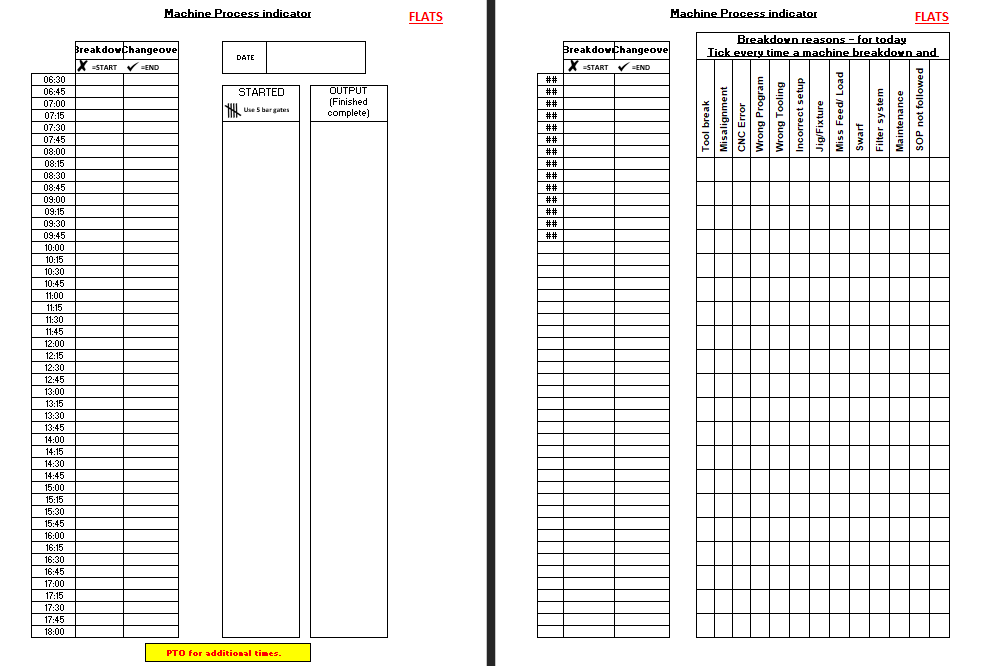
Once I have collected the data (usually on a weekly basis) I convert the data into information, in the form of charts to see the change over time, this allows us to see the impact our decisions and corrective actions have made on the system as a whole. With these charts, it’s best to put them up in the area it’s collected so the operators can see the information they themselves have had a hand in, this creates a feedback reassurance, since we can do the 10 minutes toolbox talks where the operators will talk about issues which they can then see data on in the charts.
It’s important to ask questions at the toolbox talks for both managers and the operators, we then come away with a list of actions to highlighted concerns that cannot be explained, this serves as a continuous improvement cycle where the concerns show themselves in the charts and by using the 80/20 rule we can start picking off each knowing the affect it’ll have on the whole system.
Challenges of TPM
This is keeping Total productive maintenance TPM going after you hand it over to the manager and the team – here’s were keeping things simple and straight forward (tips from a previous post) comes into play. Start with one machine /stage / process and stream line the operation that you want the operators to carry out (much like the step in SMED) by making the task take less than 15 mins to complete, there’s really no argument as to way it can’t be done (and like most of you I’ve had my fair share of arguments and reasons why they can’t find the time, perhaps they need to read my blog on Time Management ..nice plug there).
The biggest challenge I’ve come across unfortunately is that you need to have the process staffed at the correct level to ensure the operators are not feeling stressed and start removing the processes they see as time consuming (even after you’ve explained why it’s not) here I use the formula – Total process time for the line / Takt time as a rule of thumb to give me a rough idea of how many operators will make the process flow, once you have that then go ahead and implement Total productive maintenance TPM. If there’s sickness / holidays etc.. Be ready to demonstrate the simple setup you have (as I’ve had managers come in arguing they need to get throughput out the door, not realizing that the machine working today might not work tomorrow because we could have spotted the issue and had it fixed, so their throughput will suffer).
The Key take aways
To implement Total productive maintenance.
- Choose a machine to start on (probably the constraint)
- Asses it sub systems and record what they are that you intent to monitor and restore
- Conduct the condition appraisal
- Actually repair the machine to a state that you are happy to maintain
- Work out a schedule for the operators to monitor / clean and inspect the machine
- Work with the manufacturer to create a list of service parts to store and a maintain schedule for services
- Monitor the OEE for the impact and to work out the mean time to failure, then work this into the schedules.
The books in this piece are some of the many I have read to enrich and develop myself, check out my current reading list and recommendations at:
Or perhaps you would like to learn more? then I recommend my resources page:
There’s also my Engineer’s Log Book PDF download for £1.99!, get yours here:
Engineer’s Log Book PDF download
What are your thoughts? Have I covered everything or is there more you know and would like to share?
I’m always learning and improving this site and my blogs, so please feel free to get in touch with me via LinkedIn or this site to discuss any topics I have covered.
If you’re having trouble finding ways to progress check out this site filled with free learning tools: