What is ‘The Engineering design process?’
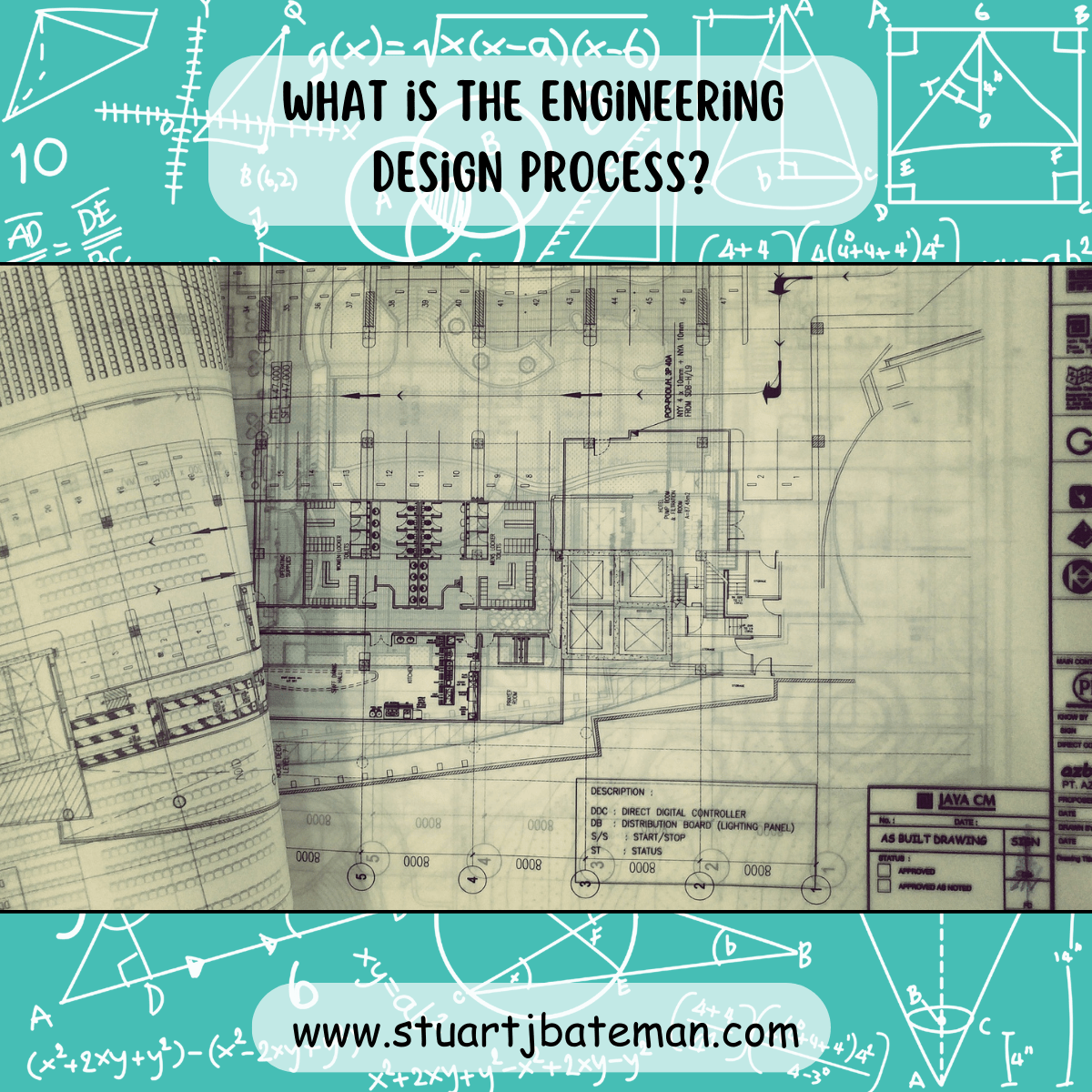
Ever wondered what the Engineering design process consisted of?
Though I might start with the title “The Engineering Design Process”, it is a design process that can be applied to any problem in any industry. When I first looked at the process back in my college days, I thought nothing more of it other than another methodology to be learnt, but now in my more experienced years I have recognised the links between this process and the scientific process.
The difference…. well, the engineering/design process starts with a problem, whereas a scientific process starts with a question, like lean and scientific thinking the design process breaks the problem/project down into manageable chunks, no different to how we tackle large problems.
Engineers apply science to the problem after defining it, and then we can establish what physical relationships we need to apply along with any constraints we need to account for (ask questions to explore the boundaries). Once this is known we design a solution based on available technology (sometimes we may need to develop the technology), again for comparison scientists start with the question move on to define it and then use their knowledge to work out how that they believe it works (after researching), after which they move on to experimentation to see if they are ‘not wrong’.
The key to the design process is in two areas, first the definition of the problem must be worked out to which we can use discussions/photos /sketches and any data to hand, only then can the second area of iteration work for us. It’s important to note that through iteration we can update the original definition as we learn more about solving the problem. After defining we ask the questions like “What physics is involved?”” What are the unknowns?” “Is this a new problem?” from which we can define characteristics to measure and collect data from for analyses. Then after we have looked over the information, we can design a solution (starting with concept designs), before moving onto testing.
It is important to note at this stage that this process isn’t an individual’s activity, it is meant to be worked by a group. A single person can start and work on it 100% while discussing the problem with those that own it, with experts that can help guide and in group activities where they foster creative solutions.
The process of iteration doesn’t just mean going through the cycle of steps but also going over the steps individually themselves before moving to the next. After testing and collecting the results we go back into the analyses mode again to see how the design fared, asking the following:
- What did/didn’t work in the design?
- Was everything accounted for?
- Was there a variable we didn’t expect?
- Did it fail? And if so, how?
- Did we gain feedback from experts/end user?
- What variable did we try to control? Did this work?
These questions allow us to update our definition and guide the next cycle in the process. Again, it’s important to retain all your work/ideas/brainstorms throughout this process as they might come into play in future iterations.
Looking at the process we can see links to Deming’s PDSA, but as within my workplace, we usually start at study before planning.
Design Process | Deming | Scientific |
Define | Plan | Observe/Question |
Research | Do | Research |
Design | Study | Hypothesis |
Test | Act | Test with experiments |
Analyse | Analyse data | |
Report conclusions |
Here I’ve highlighted how the three are similar, what this shows is that all the major processes used in industries today 8D/PDCA/DMAIC are tweaks of a process that has changed how we’ve thought about the world since the 1600’s when Newton/Kepler/Hooke/Cavendish and others first used them with great affect (and I’m sure the ancient Greeks can be credited as well).
So, where can I see examples of this today? Well, it won’t be a surprise when I say SpaceX does this with aggression. Building / Testing / Analysing and then adjust before building again. I won’t go on about SpaceX as everyone is aware of that story, however Elon’s ethic of making the design dumber by removing as much as you can until you find you really do need it, helps to keep the design simple and show the design process in action.
The question you might wonder is “Why do all the iterations in a world of 3D modelling?” can’t we simulate our way to a solution? Part of that answer is Yes, with today’s software and PC’s we can predict a large percentage of the situations we are likely to encounter (CAD helps with the conception/visualisation/ details and prototype phases to quickly iterate and produce a working idea), however how a design will fare in the real world with variables we haven’t considered for is why we test. Using processes like FMEA which Nasa developed for the Saturn V rocket helps to mitigate risks by allowing us to think of the what ifs, but our design might not be efficient, it’ll achieve the main goal at a cost of another i.e. cost/quality/delivery.
So, we must balance these within the design, which is another aspect that engineering is known for ‘compromising’ (or finding the least amount of compromised required). The other factor that may or may not be under our control is variation, yes, we will have accounted for Environment/ physics / materials for the most part, but machining/ treatments/ people/ processes & random variation can’t be all accounted for at first and via iterations we can define tolerances in expected and unexpected variables, thus testing a design to see how it performs against expectations will always be required.
To quote Feynman “If it doesn’t agree with experimental results, no matter how elegant the maths it’s wrong” – this is the same for engineering as it is for science, we need to understand if what has been designed is right or wrong and if wrong understand were it failed. This is what I believe is fitting for engineering design, test after test if it fails great! Investigate, discover and improve, you know what doesn’t work ‘Take delight in knowing you’re wrong’ as Professor Brian Cox says, in today’s environment where H&S is one of a engineers primarily concerns we should exhaust all avenues to improve a design.
For a least the last 400 years, this process has worked for us in many different versions of itself, one could argue it being one of the backbones of modern civilisation.
Resources used in this blog: –
TWI Global
Nasa
Teachengineering.org
The Essential Deming
Discoverdesign.org
My own experience
Nasa’s process
- Understand the problem & constraints
- Brainstorm all possible solutions
- Due to limitations on cost & time – pick a few ideas to test
- Built prototypes
- Test – control one variable
- Ask “How can it be improved?”
- Improve
- Ask “What did/didn’t work?”
The books in this piece are some of the many I have read to enrich and develop myself, check out my current reading list and recommendations at:
Or perhaps you would like to learn more? then I recommend my resources page:
There’s also my Engineer’s Log Book PDF download for £1.99!, get yours here:
Engineer’s Log Book PDF download
What are your thoughts? Have I covered everything or is there more you know and would like to share?
I’m always learning and improving this site and my blogs, so please feel free to get in touch with me via LinkedIn or this site to discuss any topics I have covered.
If you’re having trouble finding ways to progress check out this site filled with free learning tools:
27 October 2021 @ 16:18
helpful but boring
29 October 2021 @ 15:45
helpful
29 October 2021 @ 15:46
helpful