Why do engineers constantly use Non-destructive testing (NDT)?
The one size fits all approach of standardized testing is convenient but lazy.
James Dyson
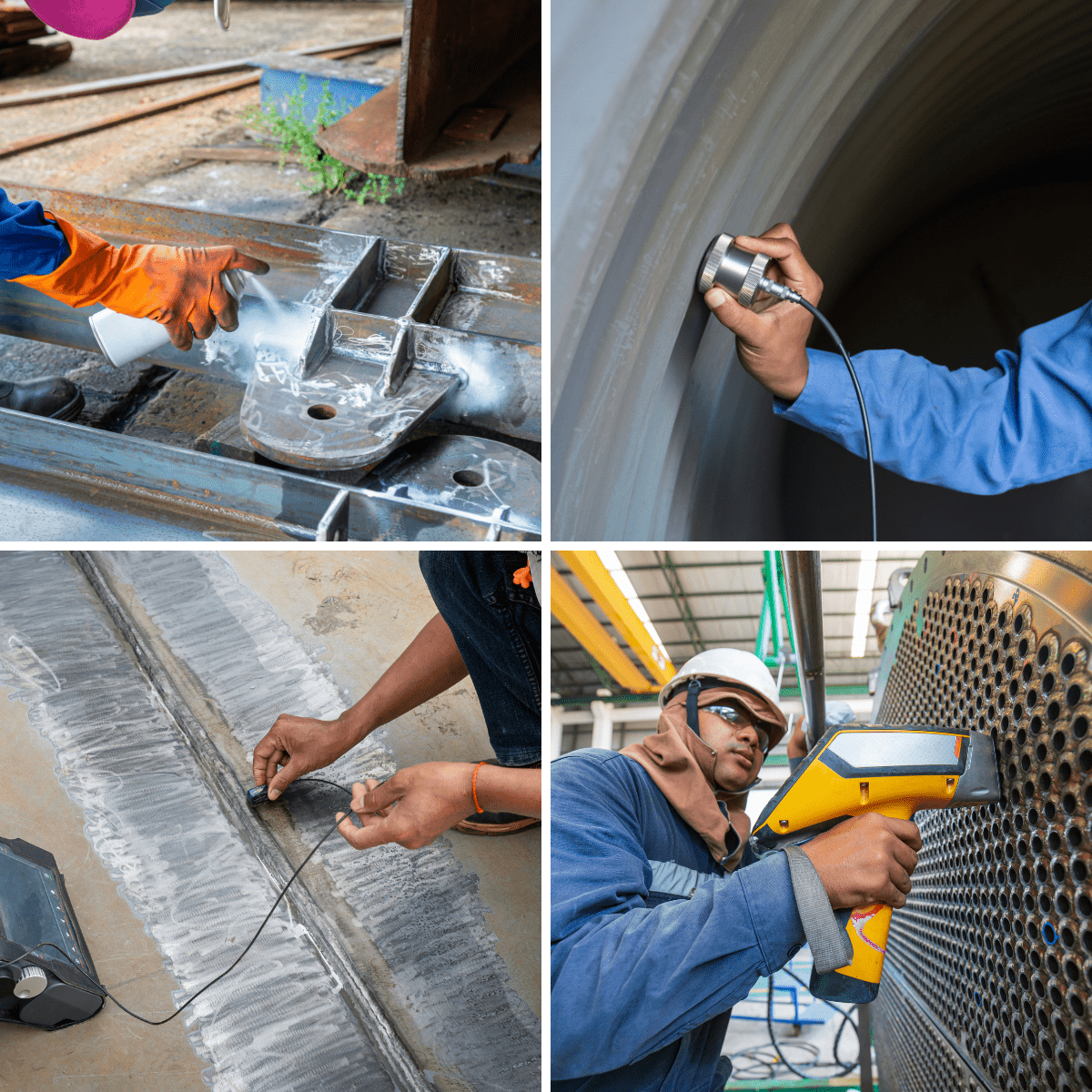
Non-Destructive Testing: Validating Without Damage
Non-destructive testing is an essential process for engineers, allowing the validation of designs, components, and processes without compromising their usability. By avoiding physical dismantling or destruction, NDT ensures that parts remain functional while providing insights into their integrity and quality.
Key Methods and Applications
- X-Ray Testing
- Primary Use: Examines welds and castings for internal defects.
- Common Issues Identified:
- Welds: Cracks, porosity, slag inclusions, incomplete fusion, and penetration.
- Castings: Air pockets, shrinkage, inclusions, and cold shuts.
- Application Example: Submarine construction, where miles of critical welds must be inspected for structural integrity.
- Die Penetrant Testing
- Highlights surface cracks by applying a dye and developer.
- Ideal for detecting fine surface defects.
- Magnetic Particle Testing
- Detects surface and slightly subsurface flaws in ferromagnetic materials.
- Ultrasonic Testing (UT)
- Uses sound waves to locate internal defects in metals, composites, and ceramics.
- Eddy Current Testing
- Identifies surface and near-surface defects in conductive materials.
- Acoustic Emission Testing
- Monitors stress waves to detect cracks and other structural changes.
- Leak Testing
- Verifies the integrity of sealed systems.
- Visual Inspection
- The simplest yet critical method, often supported by advanced tools like borescopes.
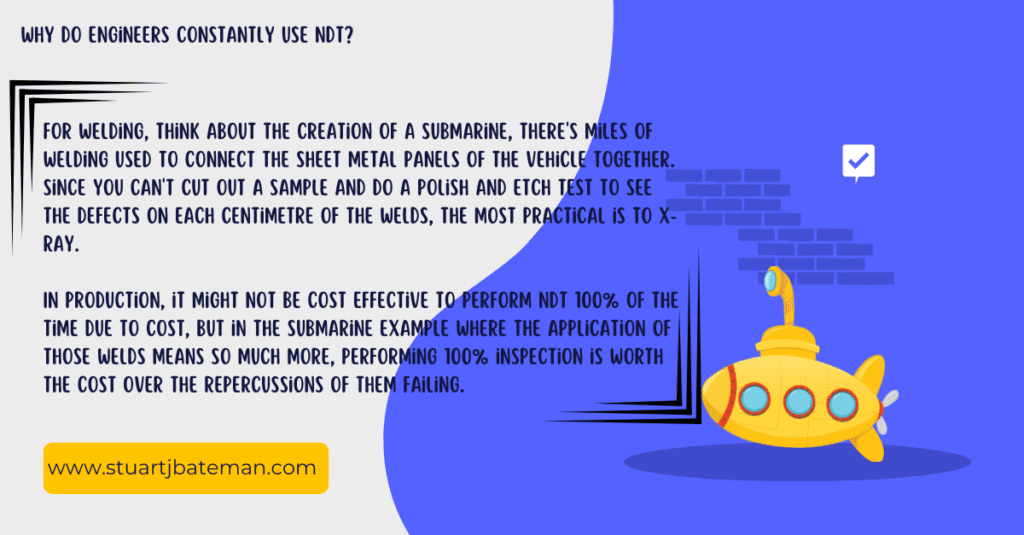
NDT vs. Destructive Testing
While destructive testing pushes designs to their limits (e.g., tensile, fatigue, or impact testing), NDT focuses on verifying parts destined for use. Destructive tests are typically performed in earlier design phases, whereas NDT ensures production consistency.
When Is NDT Applied?
- Initial Validation: During ISIR (Initial Sample Inspection Reports) or PPAP (Piece Part Approval Process) for new parts or suppliers.
- Critical Applications: For high-stakes projects, such as submarines or aerospace components, 100% NDT ensures reliability.
- Post-Defect Analysis: After detecting and correcting defects, NDT validates the fixes before resuming standard production.
- Process Monitoring: Combined with control charts, NDT provides data for statistical analysis, ensuring processes remain stable over time.
Balancing Costs and Inspection Frequency
Performing NDT on every part may not always be feasible. For non-critical applications, engineers often use sampling plans or reduced frequencies after gaining confidence through initial inspections. However, in critical scenarios, such as safety-critical welds on submarines, the cost of 100% inspection is justified by the risk of failure.
Key NDT information sources:
- ➡️ ASNT (American Society for Nondestructive Testing)
- ➡️BiNDT (British Institute of Non-Destructive Testing)
- ➡️ICNDT (International Committee for Non-Destructive Testing)
- ➡️NDT.net
The books in this piece are some of the many I have read to enrich and develop myself, check out my current reading list and recommendations at:
Or perhaps you would like to learn more? then I recommend my resources page:
There’s also my Engineer’s Log Book PDF download for £1.99!, get yours here:
Engineer’s Log Book PDF download
What are your thoughts? Have I covered everything or is there more you know and would like to share?
I’m always learning and improving this site and my blogs, so please feel free to get in touch with me via LinkedIn or this site to discuss any topics I have covered.
If you’re having trouble finding ways to progress check out this site filled with free learning tools: