A day in the life of a Production engineer – 2023
Ok, it’s about time I did one of these – S.Bateman
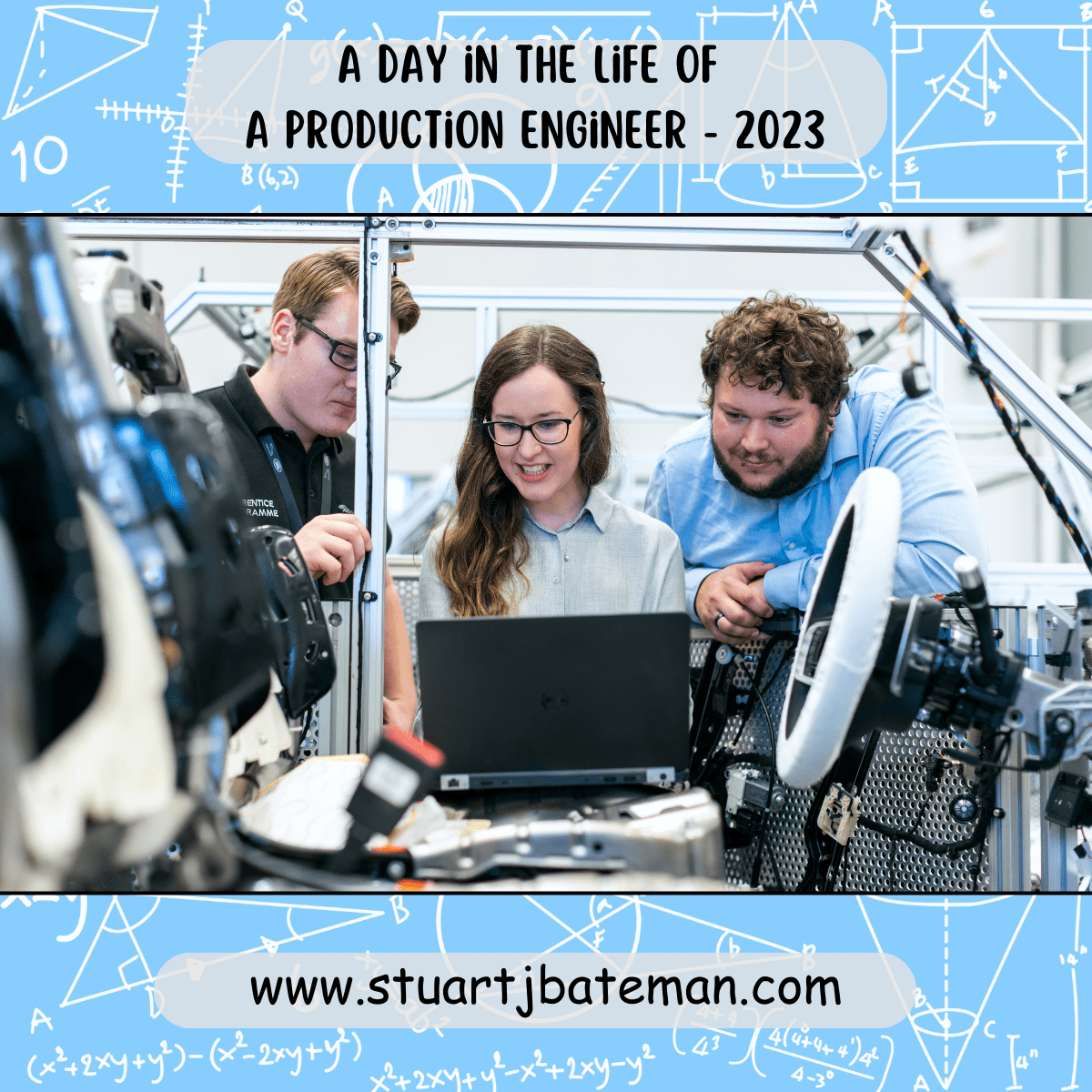
Introduction
Working as a production engineer means you have a unique set of responsibilities to fulfil, from developing and testing products to supervising production staff. Every day is different and can bring new challenges, so it’s important to stay on top of new trends and technologies to ensure you’re prepared for whatever comes your way. In this blog post, we’ll discuss the tasks a production engineer is responsible for and explore a typical day in the life of a production engineer.
After reading this post, I recommend you read my reflections on my 20 + years engineering career journey with the lessons I’ve learnt.
An Overview of Production Engineering
Production / Manufacturing and Industrials engineers are actual one in the same, however we do specialise in different fields, but originally are roots come from the same role which was industrial engineering which stems back to the days of Henry Ford and his mass production system, you could say he was the first Industrial engineer and the rest of us learnt from him.
The role splits because well.. The complexity has increase, we need to specialise in different areas while performing the improvement role, so we get Production engineers who are mainly focused on Assembly / Test and Office based systems and Manufacturing engineers who focus on the Equipment / Machines and Tools.
Here’s a extract from a great book “Materials and Processes in Engineering” by DeGarmo, Black and Kohser.
Manufacturing engineers select and coordinate specific processes and equipment to be used or supervise and manage their use. Some design special tooling that is used so that standard machines can be utilised in producing specific products. These engineers must have a broad knowledge of manufacturing processes and of material behaviour so that desired operations can be done effectively and efficiently without overloading or damaging machines and without adversely affecting the materials being processed. Although it is not obvious, the most hostile environment the material may ever encounter in its lifetime is the processing environment. The machines and equipment used in manufacturing and their arrangement in the factory also comprise a design task. Industrial or manufacturing engineers who design ( or layout) factories have the same concerns of the interrelationship of design, the properties of the materials that the machines are going to process, and the interactions of the materials and the machines.
What Does a Production Engineer Do?
Simply put the main role of a Production engineer is to look at production systems and continuous improve it, and that doesn’t mean just factory work, it means all processes – Office / shops / medical / military / civil service you name it if it has a process then a version of a production engineer with training in Lean or Sigma six will be involved. Why? It’s not just about saving costs but also time for the employees and the company, teaching employees how to improve which overall improves the working environment for all, if it can be do better / easier reducing the amount of effort while cutting the time / space / reduce number of parts / interactions, then it’s a Win : win.

A Typical Day in the Life of a Production Engineer
So now we get to the good part, what is my day like? Well, I would like to say it’s consistence but I have found in the companies that I have worked for, the role itself can be very diverse. No one day is like the last and most of my work is project based moving from one to another, but because of continuous improvement I can cycle back round to the same project again to see how things developed after the last improvement and what further ideas or requirements are needed by the company.
A ‘typical day’ would look something like this:
Starting at 6.30am, making the only coffee I have for the day I sit at my desk to study for an hour and a half. This can be reading a book or a white paper but it also includes writing up notes / ideas and further research to do, I will also alternate this time for online only courses that are related to my professional background using sites like Coursea.
At around 8am, I then write up my engineer’s log book so that I review yesterday’s tasks and what was achieve and what is outstanding. Using the format I designed, I look at the top 3 projects I’m working on and note down the next 4 priority tasks that no matter what need to be done today. Then if any jobs come up from various people and departs from yesterday I note them down using a visual management trick from the Eisenhower matrix. All my log book pages are scanned into my PC and kept online using a service like OneDrive so I’m always linked to my notes should I need to refer back to them at some point later on (This has saved me so much space after I was using A4 log books which there were 15 volumes covering 7 years sat under my desk).
This gets me to about 8.30 – 8.45am, (another tip. Since I’m always up and about, people trying to get hold of me can’t do so by ringing my desk phone, so I do call forwarding to my mobile which saves time and promotes my view that the mobile if used well is the best engineer’s tool in the 21st century). Right now I start with tasks involving any monitoring that I’m currently doing, this is any process or issue that has been reported by operators / supervisors and managers that need improvement, generally this involves tick sheets / SPC charts or videoing. Once captured I update various spreadsheets that have power query and pivot charts setup to convert the data into usable information that gets emailed back to the managers for us to review. At present the loading of the data is manual, the processing and emailing is doing via macros that I’ve programmed, next step is to design an MS access database with a user interface to capture the data and input that into excel for me…but that’s on my important but not urgent list.
So, we’re at 9am and this is when the first meeting takes place which is usually the production meeting where urgent parts are discussed with feedback from any department being chased today and items from yesterday, any issues that are being worked on and expected throughput from the assembly department. From this we have the plan on what’s expected from everyone to proceed with (this is a heuristic plan and individuals can discuss projects after this meeting). My input into this meeting will be on any Project / NPI / Jigs / Tooling and Process related work or issues.
Around 9.30am, we have the MRB (Material review board meeting) and this is the one I chair. The purpose is to review any parts that the assembly team have found with any defects on them, here we discuss the defect, what caused it, how it can be prevented, actions to be undertaken with the correct department and if the part can be saved sometimes we discuss how. If it can’t then it’s scrapped off, however if the part is from a supplier then the rework option is to reject the part back to them via the quality team and have them work with the supplier on corrective actions, here I can get involved too if a change in the process or we need better understanding of the issue.
Usually, since I also run the Toolroom I get any rework items to be address, if there are any process related issue then I take these for investigation and resolution. In the MRB we run the rule 80% agreement by the team with 100% commitment, since this is a multi-department team everyone has a voice to offer their views for consideration, but we need to made decisions to move on with.
So, now it’s 10.00am and the previous day has been dealt with and the plan for today is done. Now I get into project work and like I mentioned before this starts with completing the 4 most critical items on my log book before tackling anything else.
Presently, I’m working on several projects which includes
- Cataloguing all existing jigs / fixtures and gauges in the company that were developed before my time.
- Here I’m doing a 5S style activity and removing everything, drawing them up (since this was never done) then assigning a tooling number by engraving it onto the items, so in future we’ll know what drawings and parts refer to the item.
- After that I write a date on the jig and place it in my hold, waiting for it to be used, if after a set amount of time it isn’t then it’s removed all together and if we do need it again in the future I have the drawings.
- Increasing throughput to a new production line.
- About 2 years ago we brought a part for our final product in-house and we’ve been developing the production system for it (those of you who follow SpaceX will know about stage 0 which is the launch mount and production system which there have been many times Elon has mentioned it’s more complex than the Starship itself, it’s the same here).
- I’ve been placing the foundations of Lean with bespoke benches designed to aid with each process stage, shadowboards for the tooling and PC’s to help record measuring.
- Using VSM and time studies I’ve been checking the system to find out how the flow is working and fixing any issues I see.
- On top of that, there are a few machines that needed some unique tooling and fixturing designs to improve quality and production, which I’ve been working on, one of the best things I’ve experienced as an engineer is to see my designs manufactured and working.
- Reviewing capacity of manufacturing
- This is a new project to assess the capacity of several CNC machines within a workshop, here we need to understand the flow of parts and what decisions are being taken to manage the machines.
- This is more of an excel project to develop a spreadsheet that will give us a visually construct to the machines and what is currently loaded, where jobs are and when we expect them to be finished, basically it’s a simple MRP system. (just I’ll use macros in VBA to do the schedule and reports)
It may be 3 items, but I prefer not to dilute and focus on a small number of projects with the biggest impact on the company.
During the day I can visit several departments I’m working with to discuss the progress I’m making and any tasks I’ve set for the managers or operators to complete, Production Engineers need to be on the floor talking with all employees to get our job done. I’m never at my desk unless I’ve set aside time to work on designs, so I usually divert phone calls to my mobile so people can find me (yeah I said that above).
Since I manage projects, I have to report updates back to the stakeholders. This is done in the same way I do the data reports, unless there’s a project meeting (once a week) I email a report to them and wait for feedback, there are times when I can’t wait, so I go to those managers to get the information I need.
On occasions I work with the Engineering design teams and review the ECR‘s coming through, my job here is to look at the changes being proposed from the point of view of Production engineering – so I ask myself “Does this change require changes to the current process? Jigs / gauges / SOP / measuring systems?” if so then I need to put those systems into place or alter them for this change, at the same time I can review the change and ask for more information if it’s lacking or I see issues with it.
I also run CI (continuous improvement) hours in two areas once a week in the afternoons after lunch, this is where I promote the Lean ideas and open the floor up to the workers to present what’s been bugging them the most about the process they work within (yes this needs steering at times), however the best and major improvements I’ve helped with is when I’ve been given the idea from those who work the process see the Production trolley CI project.
At the end of the day, I look back at my log book to see what’s been ticked off and what new tasks / issues have been reported back to me as this will then form the log book list tomorrow along with the next steps for the projects I’m working on (these tasks will either come from an Action Plan or VSM or Project charter). This usually takes up the last 30 mins of my day and is something I strive to make sure I do, however there have been many pop up meetings or problems that require my attention.
So, that’s it a typical day for A Production Engineer, I’d love to hear from other Production Engineers and their days so please comment below.
The Benefits of Being a Production Engineer
I’ll list here the benefits I see for myself and hopefully they’ll resonate with you.
- The problems I face daily aren’t the same as before, there’s always something new to solve.
- Working within manufacturing, I get to see how things are made, I get to speak to other companies and visit them to see their processes and the limits of current technology.
- 9 out of 10 times, the engineers you work with will have a similar mindset to you, and there are times when I’ve solved problems by just bouncing an idea or discussion with a group of engineers, it’s amazing the thoughts and experience they have to help find a solution.
- I get to work in a variety of industries as they all need improving.
- I get to create and design new tools and processes to make products for people.
- I get to improve the working lives of the people within your company’
- Innovation is part of the job and the most rewarding aspect, you get to create and not consume. This leads on to a lifestyle of creating things to benefit yourself or others.
- I get to work within a team environment.
- I get to design things and experiment using the scientific process to find route causes or to discover how your solution will work in practise.
Preparing for a Career in Production Engineering
I have spoken at length about this topic and honestly there is no one route, I talked to veteran’s coming out of the Navy on their visit to Stannah about a career as an Manufacturing engineer and I’ve spoken to college students from HSDC about engineering in factories, and the route can be different as in my view an engineer with a degree is no different to one with 20 years of on the job experience.
So where do I advise you start, it depends (I do say that a lot but it’s true) on where you’re coming from – School / College / Uni / Forces or a different industry there are many routes to becoming a Production Engineer. Traditionally, PE’s were engineers who worked on the production lines and developed skills and ideas to improve it, there are many PE’s out there who don’t have degrees but rather they have years of good engineering experience (as we all think alike remember?).
The route I took was school – college – university and then into a manufacturing company, from there I worked on scheduling jobs until a position as a CNC programmer came up which I took, that was when I met a Production engineer who I learnt about Lean. After having 5 years’ experience in manufacturing I applied for a job as a manufacturing engineer at Stannah, they gave me the room to grow and learn more about the PE’s role from several very experienced engineers. Before long I took on another opportunity at AI to see if I could start a PE department from scratch and develop a production line from what I learnt, and trust me I found the gaps in my knowledge!
Ok, your route, depending on where you start the best thing you can do is get experience. Having an engineering education is great but you can train yourself within a job that’s related, again see my post about mentors. Next getting a job in a manufacturing company is a good start, but any company should doing a level of continuous improvement, so you need to join one of them and get into the groups / projects that’s focussed on developing / improving something (either that or look for improvements yourself and suggest them). Be interested and take note of how projects are run, talk with the engineers and work with them to develop yourself to how they think and work, this can take a few years but have several projects under your belt will aid you in moving onto a role which is more engineering focussed (this might be within you current company or at another).
Like I said at the beginning, many engineers have years’ worth of experience and many have an academic background, some have had apprenticeships (another great way) and many others have had part-time jobs that are engineering focussed, and others come from industries that are related. Choose one of these to start your career.
Conclusion
Production engineering is a rewarding career path that can be highly beneficial to workers who are seeking a career where they can make a positive impact. It requires dedication, skill, and expertise, but the rewards are great. A production engineer is responsible for overseeing the production process, testing and developing products, supervising production staff, and staying up-to-date on new trends and technologies in the industry. With the right training and preparation, a day in the life of a production engineer can be highly rewarding and satisfying.
Resources:
https://www.engineeringtoolbox.com
https://www.gdandtbasics.com/gdt-symbols/
https://www.twi-global.com/technical-knowledge/faqs/what-is-industrial-engineering
The books in this piece are some of the many I have read to enrich and develop myself, check out my current reading list and recommendations at:
Or perhaps you would like to learn more? then I recommend my resources page:
There’s also my Engineer’s Log Book PDF download for £1.99!, get yours here:
Engineer’s Log Book PDF download
What are your thoughts? Have I covered everything or is there more you know and would like to share?
I’m always learning and improving this site and my blogs, so please feel free to get in touch with me via LinkedIn or this site to discuss any topics I have covered.
If you’re having trouble finding ways to progress check out this site filled with free learning tools: