How can we prevent Mistakes in Manufacturing.
Understand the power of positive feedback loops- The road ahead
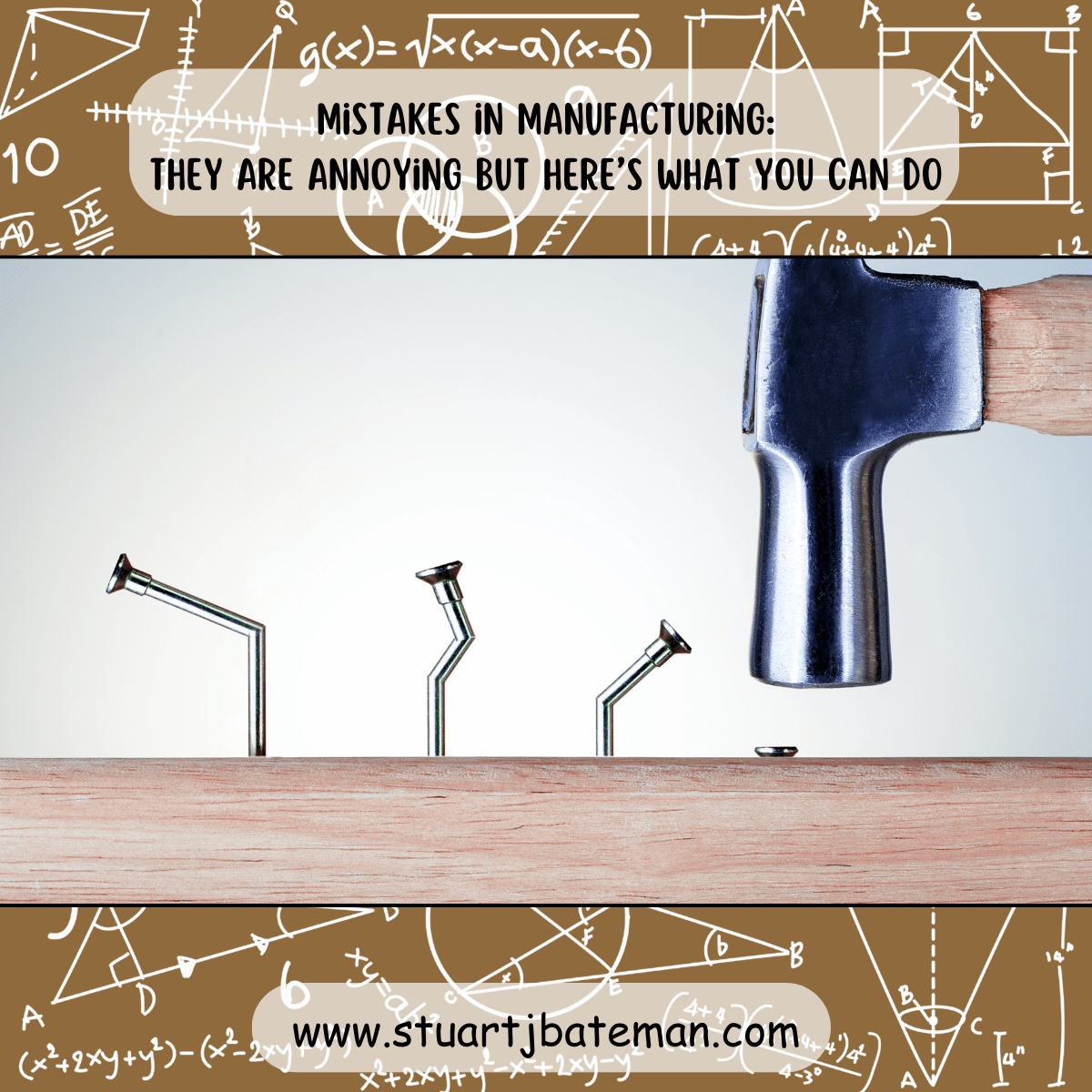
Why are there some many mistakes in manufacturing that have to be fixed?
Mistakes happen everywhere (we’re only human after all) and even in manufacturing they can happen from the simple miss screw to ones that cause defects on products to unfortunately the ones that can harm others, it’s important to address any mistakes that are found.
So, what are mistakes in manufacturing, these are operator choices that happen because the process in itself is broken and has allow the choice to happen since the operator/manager/supervisor wants to do a good job and get product out the door, they also occur from aspects outside our control.
In this article I want to address how to identify mistakes, what they can be and how I have captured/analysed and then moved on to eliminating or controlling them so that they are not repeated.
Mistakes in manufacturing come from poorly designed processes as a result of NPI implementations, these introduce new production lines or more parts/products into existing lines, or can be a solution for another problem that has caused this new mistake to happen, overall the process needs to be reviewed and improved.
But let’s not restrict mistakes to those that happen on the shopfloor, they can happen within any department of a company (engineering, finances, operations, goods-in, packaging, machine shop) all with their own problems that cause them, the methods I highlight below will work in those areas too.
Identify/Detect
- How to ID mistakes:
- Go work on the line and review the process first hand
- Talk to operators
- Video the processes
- Learn by doing the job yourself
- Start a Non-conforming report system to capture parts that are damaged and the reasons why
- Collect data from all these and populate a pareto chart to understand frequency
- Review any PFMEA’s or if none exist create them and ask the operators/supervisors and managers involved with the process to weigh in
- Understand what controls are in place to capture and detect mistakes
- Train operators to spot mistakes in the process and highlight them to production engineering
- Remember this can bet effective as a buddy check, with no blame since the process allows for the mistake to happen
- Start an Out of box measure from your distributors (captures packaging issues)
- Metric monitors like those highlight in this post about The Visual Factory
- Bring in a 3rd party for a process audit, they could have a focus on H&S or Manufacturing in general, so be sure to think about where you want them to focus their efforts.
- Benchmark your processes from other suppliers, doing trips to other suppliers/companies and even to the conventions gives you the opportunity to ask them what troubles they’ve had and what solutions were used, if they have similar processes to you it’ll help you to check if you have the same problem.
- 5Y – This process is by far the easiest and quickest to implement, while at the same time yielding a significant impact on identifying problems.
- This works best with processes like NCR’s (Non-conforming reports) where we start with the problem statement and ask Why?
- But more importantly, this is one of the processes where we can get the operators involved with coming up with solutions to solve the problems they face, which helps buy-in and take up of the end solution
- Ishikawa can be used, but these are best used after the mistake has taken place. Mainly used to identify route causes,
- Go work on the line and review the process first hand
- Types of mistakes(but not limited to):
- Dropping items – damage
- Losing items
- Incorrect measuring
- Part Contamination
- Manual tools (miss hits)
- Incorrect use of tools / jigs and gauges
- Poor instructions
- Wrong programs used
- Wrong materials loaded
- Wrong revisions of drawings used
- Drawing related errors not caught on reviews
- Changes in operators (new ones)
- Not following Safety measures
- And many more..
Analyse and Prioritise Mistakes
- SPC
- Normally for machines, special cause variations that can be spotted on a SPC will enable managers to ask the question “What happened?” – this will lead to errors
- Control charts
- Tracking problems over time will help lead to causes when they happened
- NCR’s
- Training operators to raise Non-conforming reports allows them to highlight where in the process the mistakes are happening
- Pareto charts
- This helps us prioritise problems – remember 80% of the problems comes from 20% of the input
Control and Eliminate
- Methods we can employ to highlight and correct mistakes
- One of the most well-known is Poke-Yoke which can identify and deal with non-conforming parts
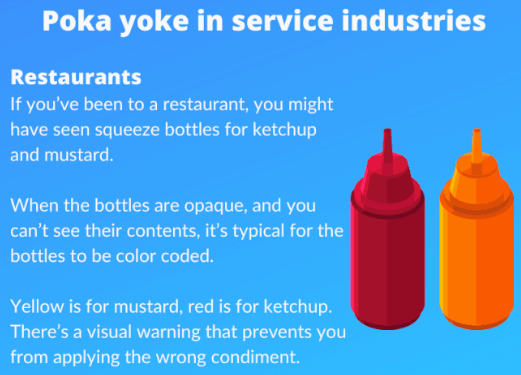
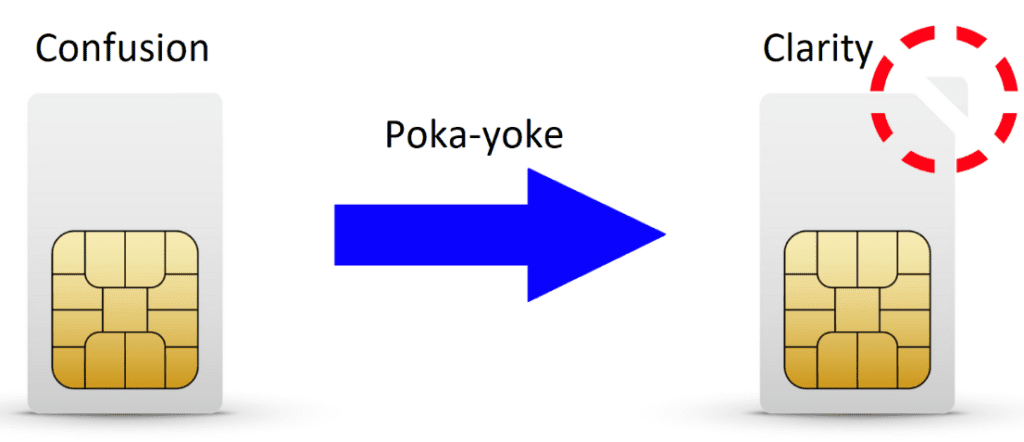
- Continuous improvement is another method to reduce/eliminate mistakes, by reviewing a process and improving aspects of it (like removing the need for steps/tooling/handling) we can automatically remove mistakes as well.
- Six-sigma is another well-known process that surgically analyses processes that are constantly producing defects to fine tune by identifying significant relationships by inputs and outputs
- Designing systems off line with the help of operators allows you to identify mistakes/problems before implementing process/production lines
- Visual management with Standard work instructions, again we need to give the operator the information they need to make the correct decisions include what to do in a non-conforming situation, here instructions can be updated with the mistake that was found and what to do about it if found again. Visual controls are great here to convey information with signs/pictures or signals to correctly direct the operator to perform the task in the way it’s meant to be done.
- As mentioned in the identifying section, creating effective PFMEA’s will help highlight potential process complications and the potential for mistakes, again using a multidiscipline team we can mitigate and implement control measures.
- Automation, so I will address the elephant in the room. The last resort that I believe should be implemented is automating the process to eliminate the mistakes. For this to be done, I would say there would have to be a significant case that the process can’t be made to function correctly using skill operators, that or the process is simple enough that automating it eliminates other issues.
- Last, we should put in a monitoring metric on the process to watch it over the next period of time (agree by the department) so that any deviations are quickly captured and escalated.
- Metrics include:
- KPI
- Defect rates
- Yield
- CT
- Throughput
- Metrics include:
Conclusion
It’s important to note that while I’ve talked about in-house mistakes, there are defects and problems of a similar nature that come from supplier parts, which you can use the methods above to help them improve and solve their problems. Like with Toyota, they like to support and grow with their suppliers that fosters a healthy collaborations and openness.
Resources:
https://www.tacton.com/cpq-blog/how-to-reduce-manufacturing-errors
https://www.dozuki.com/blog/best-methods-to-reduce-human-error-in-manufacturing
The books in this piece are some of the many I have read to enrich and develop myself, check out my current reading list and recommendations at:
Or perhaps you would like to learn more? then I recommend my resources page:
There’s also my Engineer’s Log Book PDF download for £1.99!, get yours here:
Engineer’s Log Book PDF download
What are your thoughts? Have I covered everything or is there more you know and would like to share?
I’m always learning and improving this site and my blogs, so please feel free to get in touch with me via LinkedIn or this site to discuss any topics I have covered.
If you’re having trouble finding ways to progress check out this site filled with free learning tools: