How to go about implementing Continuous Improvement.
People are usually eager to give and implement improvements ideas if they don’t threaten job security. – Creating continuous flow
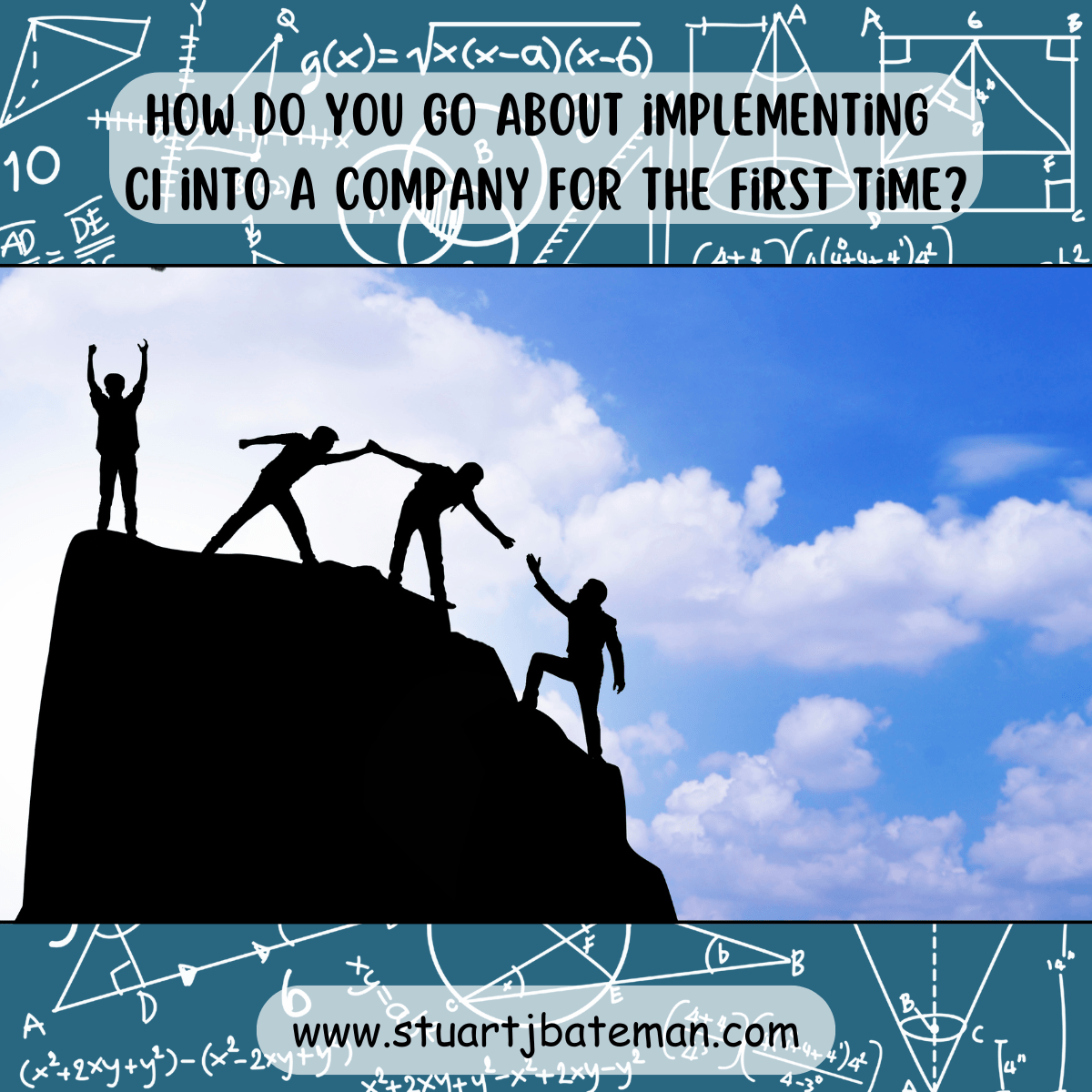
Implementing Continuous Improvement in a New Environment
So this is it, you’ve spent several years in a top company with a team of engineers who have everything worked out with best practises and a positive learning environment where you’ve been able to learn all the methods and techniques of Lean and Six Sigma including Continuous Improvement with the help of the work force who are positive and contribute meaningfully to the projects and improvements you put forward.
Now, you’ve decided to break free from that company and venture out into the unknown wilds of industry to make your own mark on the next business you join, one where all this doesn’t exist and you’re given a clean white sheet of paper to design the system you want / believe this company deserves to take it into the 21st century.
So, what’s your next step? How do you go about implementing a CI culture in a company who’s never had much opportunity to experience the power of the workforce improving their environment and company, let’s have a look at my journey and see.
Step-by-Step Guide to Establishing Continuous Improvement
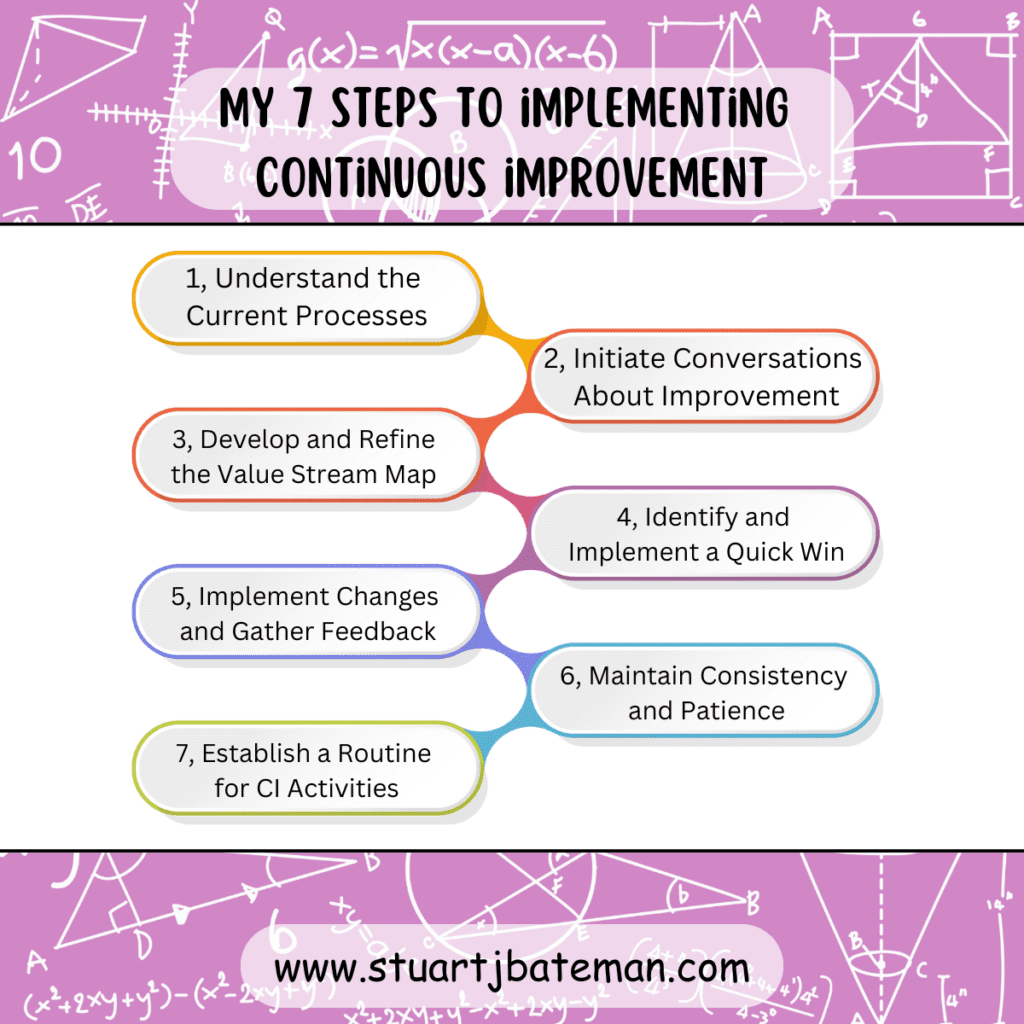
1. Understand the Current Processes
- Spend substantial time on the shop floor observing and participating in daily operations.
- Engage with operators by asking key questions:
- Why is the process done this way?
- Have alternative methods been attempted?
- How is correctness ensured?
- What issues have occurred previously?
2. Initiate Conversations About Improvement
- Discuss the current challenges operators face and explore potential improvements.
- Regularly introduce and reinforce available methods for enhancing processes.
3. Develop and Refine the Value Stream Map
- Create an initial Value Stream Map (VSM) of current processes and seek operator feedback for accuracy and insights.
4. Identify and Implement a Quick Win
- Choose an issue that can be quickly addressed to demonstrate the effectiveness of CI principles and your commitment to listening to operator concerns.
5. Implement Changes and Gather Feedback
- Actively seek and promptly address feedback from workers during and after improvements to ensure the changes meet their needs.
6. Maintain Consistency and Patience
- Regularly visit the department to discuss ongoing and upcoming improvements, reinforcing the CI process and its benefits.
7. Establish a Routine for CI Activities
- Start with a weekly CI hour, eventually transitioning to monthly sessions as routines solidify.
- Educate staff on Lean principles and the importance of quick wins.
- Encourage and prioritize suggestions for new projects in collaboration with area managers.
- Continually refer back to the VSM to monitor improvements and benchmark key metrics like cycle time and waiting times.
- Gradually introduce broader systemic changes such as flow optimizations, pull systems, visual management, and Kanban, ensuring operators are ready and willing to support these enhancements.
Philosophical Underpinnings and Inspirations
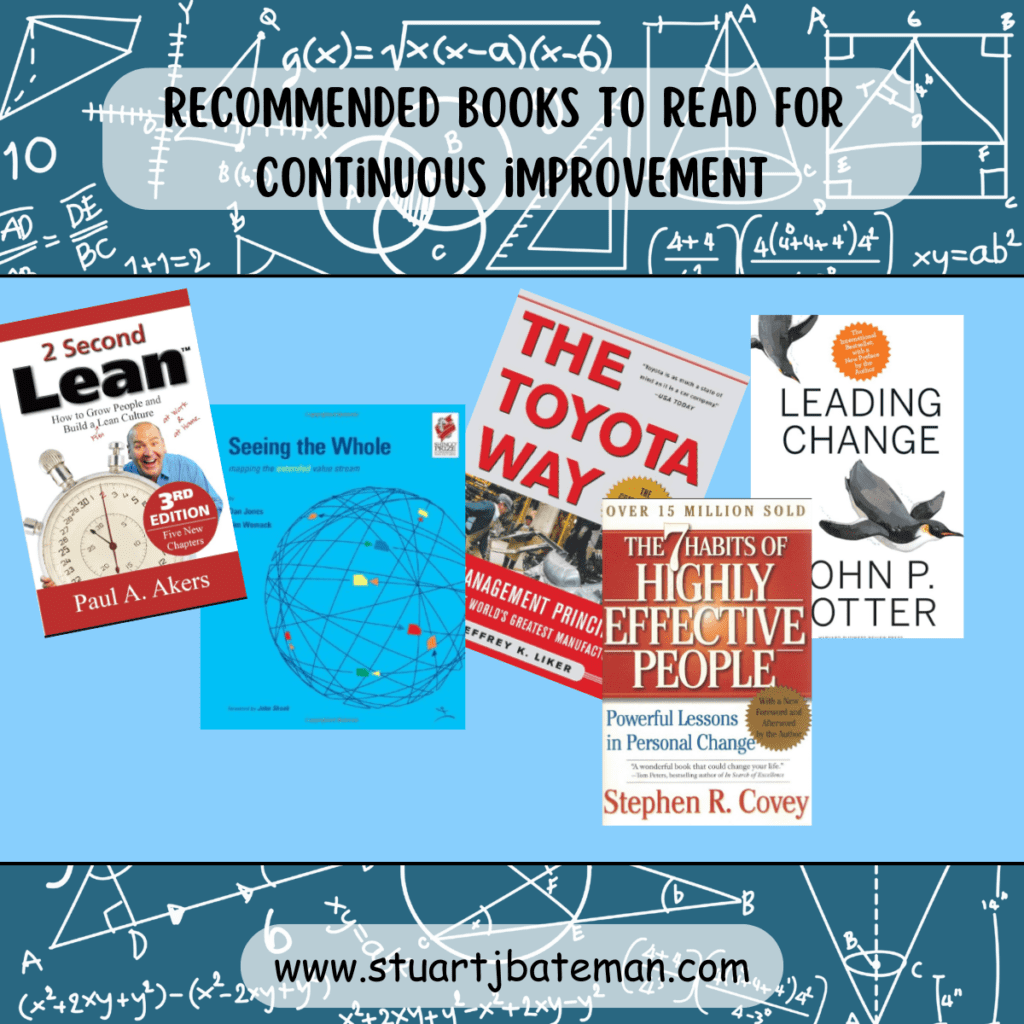
The ideas are simple, operators need to understand and be a part of what CI is all about. Then they can drive the changes, they won’t always be on the same level as the system ones, but it’ll matter to them.
By educating them to see waste and empowering them by encouraging them to develop the ideas/solutions they need, it aligns operators to the improvement process, and thus accelerates change.
The process I use above is inspired by several books and people:
- John Kotter’s “Leading Change”
- The idea of quick wins gains the operators trust that you’ll address their concerns
- Paul Akers “2 second lean”
- The idea that every day we can improve things just by taking 2 seconds off a process, the power of small incremental changes
- Jeffrey Liker’s “The Toyota way”
- The idea of educating the operators to enable them to be your change agents and change team.
- Jones, Womack and Shook “Seeing the Whole”
- The idea of creating a guiding map for the improvement process, and taking the time to benchmark and update
- Stephen Covey “The 7 Habits of highly effective people”
- This practises habit 2 & 3
- Start with the end in mind – VSM future state
- Put first things first – Start with the quick wins and help the operators, then move towards the future state.
- This practises habit 2 & 3
By educating and empowering operators to see waste and develop solutions, this strategy aligns all team members with the improvement process, accelerating sustainable change and fostering a robust Continuous Improvement culture.
The books in this piece are some of the many I have read to enrich and develop myself, check out my current reading list and recommendations at:
Or perhaps you would like to learn more? then I recommend my resources page:
There’s also my Engineer’s Log Book PDF download for £1.99!, get yours here:
Engineer’s Log Book PDF download
What are your thoughts? Have I covered everything or is there more you know and would like to share?
I’m always learning and improving this site and my blogs, so please feel free to get in touch with me via LinkedIn or this site to discuss any topics I have covered.
If you’re having trouble finding ways to progress check out this site filled with free learning tools: