What is Flow Production? Complete Implementation Guide + Real Examples 2025
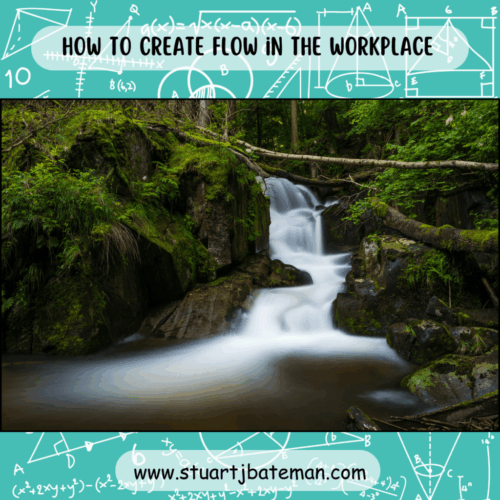
Teach others so that you’ll learn more – Rich Dad / Poor Dad
What is Flow Production? (Updated for 2025)
Flow production is a manufacturing method where products move continuously through sequential workstations without stopping or waiting in queues between processes. This streamlined approach, which gained popularity in the 1920s, eliminates waste by ensuring the smooth movement of information, operators, and materials throughout the production line. Unlike batch production where items wait in queues, flow production focuses on one-piece flow – allowing finished items to immediately move to the next stage without delays.
Table of Contents
- Section 1: What is Flow Production? (Expand Definition)
- Section 2: Flow Production Benefits and Advantages
- Section 3: How to Implement Flow Production
- Section 4: Flow Production Tools by Implementation Phase
- Section 5: Flow Production Implementation Challenges & Solutions
- Section 6: Real Flow Production Success: Stannah's Flow Production System
- Section 7: Flow Production vs Batch Production Visual Comparison
- FAQ Section
- References
Section 1: What is Flow Production? (Expand Definition)
Flow production is fundamentally about eliminating hindrance to three critical flows:
- Information flow – Clear communication and instructions
- Operator flow – Smooth workforce movement and task transitions
- Material flow – Continuous movement of parts and products
The goal isn’t to set Takt time (that comes with Pull systems) – it’s to identify and eliminate anywhere that flow stops.
Key Principle: Where flow stops is where you focus your attention.
Section 2: Flow Production Benefits and Advantages
Immediate Flow Production Benefits:
- Increased throughput – More products completed per day
- Faster delivery times – Products complete without waiting for entire batches
- Reduced work-in-progress (WIP) inventory
- Lower cycle times – No queue time added to process time
- Better quality control – Issues identified immediately, not after entire batches
Check out this video I found that illustrates the key differences between batch and flow production.
As you can see, doing one piece at a time allows for one finished item to be done without having to wait for the entire batch to be ready, in many cases we would add Queue time to the cycle time for batches which increases the process time. Since there is no queue the item once completed is free to move on to the next stage.
A quick note, flow does rely on time study analysis to find constraints and line balance product at each stage, to understand cycle times we need to conduct Time studies. While you get to grips with that, this video shows you how a flow production line will work after you’ve implemented the recommended actions.
Section 3: How to Implement Flow Production
I use this proven framework adapted from Katie Mackle’s work:
Step 1: CREATE Flow
Focus: Material Movement
Process:
- Study the current process – Conduct observational studies
- Map out current process sequence
- Identify bottlenecks and delays
- Apply 3S methodology – Sort, Sweep, Shine
- Remove obvious wastes at each workstation
- Organize tools and materials for efficiency
- Create Value Stream Map (VSM) – Visual process analysis
- Get holistic view of entire production line
- Identify improvement opportunities
Key Tools: Theory of Constraints (TOC), Total Productive Maintenance (TPM), Single Minute Exchange of Dies (SMED)
Step 2: MAINTAIN Flow
Focus: System Stability
Core Areas:
- Reduce Complexity – Simplify parts and processes where possible
- Control Variation – Standardize processes to reduce unpredictability
- Prevent Mistakes – Build in error-proofing (Poka-yoke)
Why This Matters: Even the best flow system fails without stability
Step 3: ORGANIZE Flow
Focus: People and Information
Implementation:
- Visual Management – Make problems visible immediately
- Standard Operating Procedures (SOPs) – Document best practices
- Process Monitoring – Track key metrics continuously
- Continuous Improvement – Regular review and optimization
Critical Success Factor: This order matters – you can’t organize what doesn’t flow!

Section 4: Flow Production Tools by Implementation Phase
Depending of what you’re trying to improve within the production line, I recommend using the following tools to help with each stage. Be sure to conduct a VSM to help identify what is hindering your flow (just like using the Theory of Constraints) find the flow constraint and eliminate it.
Creating Flow (Material Focus):
- Availability (OEE) + Heijunka + Line Balancing
- 7 Wastes identification + Capacity analysis
- VSM + Buffers + TOC + Kanban
- Yield & Supply volatility management
- TPM + SMED implementation
Maintaining Flow (Machine Focus):
- Performance (OEE) + Variation/Complexity reduction
- Machine-part matrix + Poka-yoke systems
Organizing Flow (People Focus):
- Quality (OEE) + SOPs + Visual Management
- 7 Quality Control tools + 5S + Layout optimization
Section 5: Flow Production Implementation Challenges & Solutions
I’ve come up against my fair share of cultural related resistance, and it’s never easy to overcome, nor is it wise to just ignore it, below are some of the actions I’ve taken to ‘adjust’ for the challenges to adapt for flow.
Flow Production Challenge 1: Cultural Resistance
Problem: People resist flow production changes and optimize individual workspaces Solution: Include operators in flow production problem identification, explain flow production benefits clearly
Flow Production Challenge 2: System Constraints
Problem: Bottlenecks disrupt flow production, especially when upstream Solution: Use Theory of Constraints and Line Balancing to address flow production timing issues
Flow Production Challenge 3: Supply Chain Coordination
Problem: Suppliers can’t support flow production Just-in-Time delivery requirements Solution: Work with suppliers on their Lean initiatives to support flow production
Flow Production Challenge 4: Inventory Management
Problem: Flow production requires precise inventory timing Solution: Implement robust supplier relationships and backup plans for flow production
Section 6: Real Flow Production Success: Stannah’s Flow Production System
My own experience with flow – from Stannah……
Stannah had one of the best flow systems that I’ve seen (and I’ve been to Siemen, Rangemaster, Wilson tools, Yamazaki Mazak and several others), what puts their flow system ahead is the level of organisation and availability on the production lines.
Everything they need is within arm’s reach, Computers tell them what to build next at the start of the line and there’s a PC and testing at the end (this is the same on each line), there are overhead air tools that operators reach for, the work instructions are laid out just above their heads, the parts are fed into gravity racking system so the parts roll forward and are at waist height, the line have a chain driven system that the carriage ride on and it’s these carriages that the product is built on and travels down the line, the line itself is configured so depending on staffing it can be switched from a 3 to 4 to 5 or even 7 stage operation (all line balanced), parts are delivered by material handlers who service designated lines on a schedule. If you want to see flow there’s no better example in my opinion.
What Made Their Flow Production Work:
- Everything within arm’s reach
- Automated work instructions
- Gravity-fed parts system
- Flexible line configuration (3-7 stages)
- Scheduled material delivery
Key Takeaway: The best flow systems combine organization, availability, and flexibility.
Section 7: Flow Production vs Batch Production Visual Comparison
Flow Production is a production method that has been used for the last century to help increase production and streamline processes. It can be a powerful tool for businesses to achieve higher output and more efficiently complete production processes. By understanding what Flow Production is, the benefits it offers, and how to implement it, businesses can make sure they get the most out of the method.
Here’s the final visual I wanted to show, you can clearly see that flow enables you to remove the waste of waiting for products to move onto the next stage, either to another process or to a customer, If you could do me one favour next time you’re in McDonalds or a fast food chain, take a closer look at their kitchen as they are one of the best flow line producers! – In approx. 45 secs..

The Bottom Line: Flow production eliminates waiting waste – products move immediately to next stage or customer.
Pro Tip: Study McDonald’s kitchen next time you visit – they’re masters of flow production (45-second order fulfillment)!
FAQ Section
Q: What is flow production in manufacturing? A: Flow production is a manufacturing method where products move continuously through workstations without queuing or waiting between processes.
Q: What are the main benefits of flow production? A: Key benefits include reduced cycle times, lower inventory, faster delivery, better quality control, and increased throughput.
Q: How do you implement flow production? A: Follow the three-step framework: Create flow (focus on materials), Maintain flow (focus on machines), and Organize flow (focus on people).
Q: What’s the difference between flow and batch production? A: Flow production moves items continuously one at a time, while batch production processes groups of items together, creating queues and delays.
References
As always, I have added Amazon links to these references so you can investigate and get your own copy of their works for you to enjoy and develop yourself with, these links have no cost to you but I will gain a small commission, should you decide to purchase.
- The Lean Toolbox – Bicheno & Holweg
- The Goal – Eliyahu M. Goldratt
- Creating level pull – Art Smalley
- Making materials flow – Rick Harris
- Seeing the Whole – Jones & Womack
- Creating Continuous Pull – Mike Rother & Rick Harris
- TPM – the western way – Peter Willmott
- The Visual Factory – Michel Greif
- Flow Engineering – Steve Pereira
Just links.
- AW Schultz
- Treston USA
- Thinkflow innovations – Katie Mackle
The books in this piece are some of the many I have read to enrich and develop myself, check out my current reading list and recommendations at:
Or perhaps you would like to learn more? then I recommend my resources page:
There’s also my Engineer’s Log Book PDF download for £1.99!, get yours here:
Engineer’s Log Book PDF download
What are your thoughts? Have I covered everything or is there more you know and would like to share?
I’m always learning and improving this site and my blogs, so please feel free to get in touch with me via LinkedIn or this site to discuss any topics I have covered.
If you’re having trouble finding ways to progress check out this site filled with free learning tools: