How should you start in the lean manufacturing journey?
What I wanted to know 15 years ago when I started
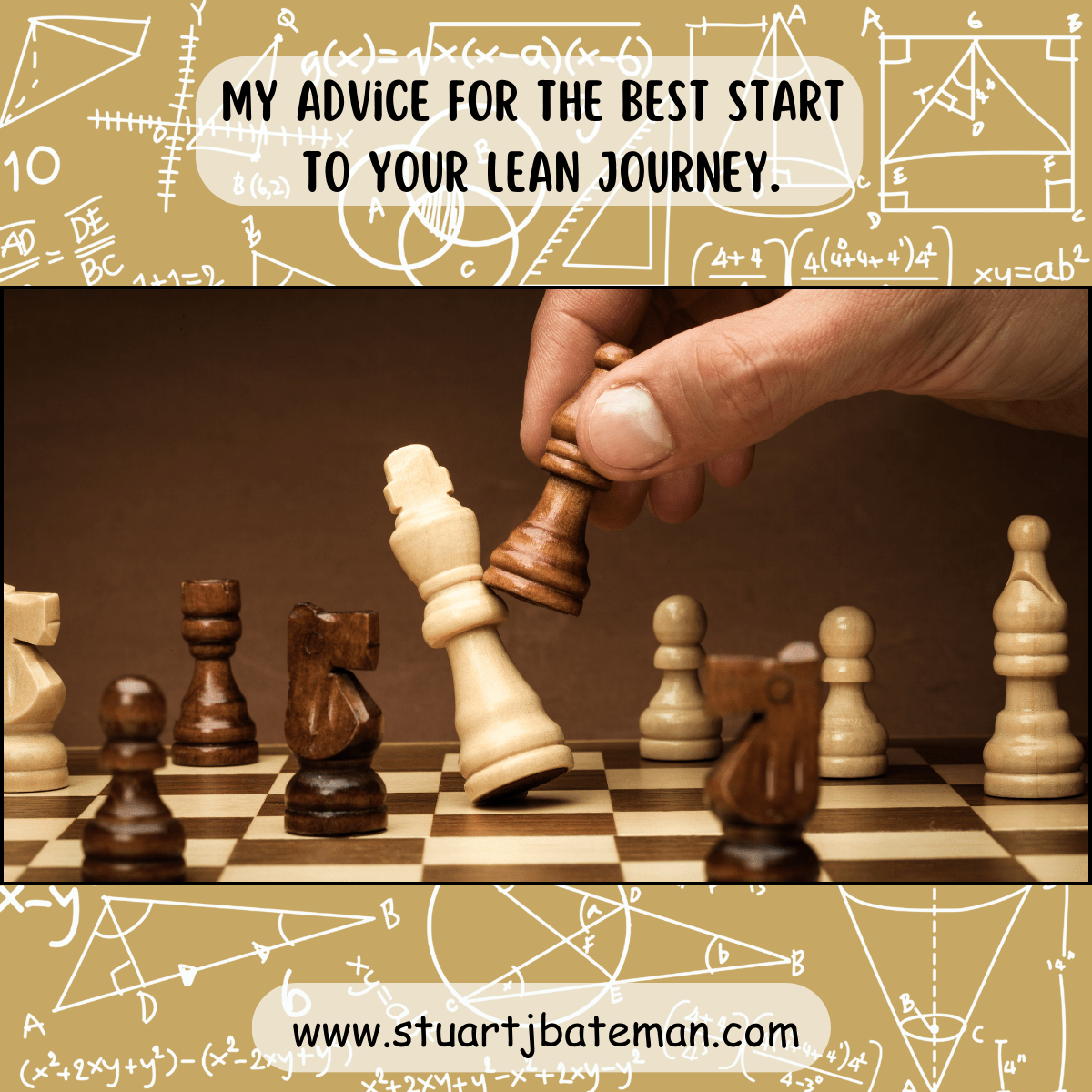
Refreshed after a 2 week holiday lets catch up! and dive in Lean Manufacturing.
How should you start in the lean manufacturing journey?
Interesting question, where does anyone start with a topic they haven’t come across before? Well, an answer would be to find a mentor (next month’s topic), but if that option isn’t available where else is?
When I started at Stannah I was faced with this very question, I needed to study and learn lean manufacturing while doing daily tasks, so I reached out to previous colleagues from my last role at Lewmar and one of them recommended the book “The Lean Toolbox” it helped her at Goodman’s. Again, if you don’t have a network try LinkedIn as there are 100’s of experts and groups who can start you off. But in this article let me share my experience in the hope that it will give you some ideas what to do next in your development.
So, I started a daily routine of studying for an hour a day (at work) and testing out what I had learnt, another benefit at Stannah were the 6 other manufacturing engineers that I could bounce ideas off and obtain that valuable feedback I’ve spoken about before. The lean toolbox is a fantastic book but what helped link the brief explanations of the tools together was the book “The Machine that changed the World” and “The Goal” – go try them as you can pick these up for next to nothing second hand from eBay or Charity sites.
So, two big ideas of Lean Manufacturing: –
- Waste management
- Constraints
Which contribute to that sacred ‘Flow’ status we desire on our production lines. As always, many others have covered the details, so I encourage you to research them as you please.
The main idea I want to highlight to you is that of Flow, this is the main aim of most manufacturing & service industries and the tools in Lean Manufacturing help us to remove the road blocks that get in the way.
Flow (Order that I use the Lean Manufacturing tools to tackle flow): –
- Activity / Time study baseline
- 5S
- Visual management
- SOP
- 7QC
- TPM
- Activity / Time study baseline after
- Constraints
- Waste – CI
As you move through production areas removing waste you must also implement the above to aid flow, we can use TOC (Theory of Constraints) to find the processes that require our focus & these tools first (keep it simple, at the start as constraints will be easy to spot, later we’ll use Pareto / Ishikawa to find others).
I’ve ordered the tools above which I will go into next, but as a note I tend to employ these tools first before going deeper into processes and using SMED / kanbans / kaizens / pull / heijunka etc…
Starting the improvement process
Start by bench marking the process in its current state, conduct time studies to understand expected cycle times and activity studies for the performance metrics along with what’s actually taking up the hours. Study the que time of parts waiting next to the process – how does that change daily/weekly?
What’s the customer demand – work out your takt time. From this we can create the current state VSM and the basics of little law (WIP = Lead time x Throughput), this comes in handy later when balancing processes.
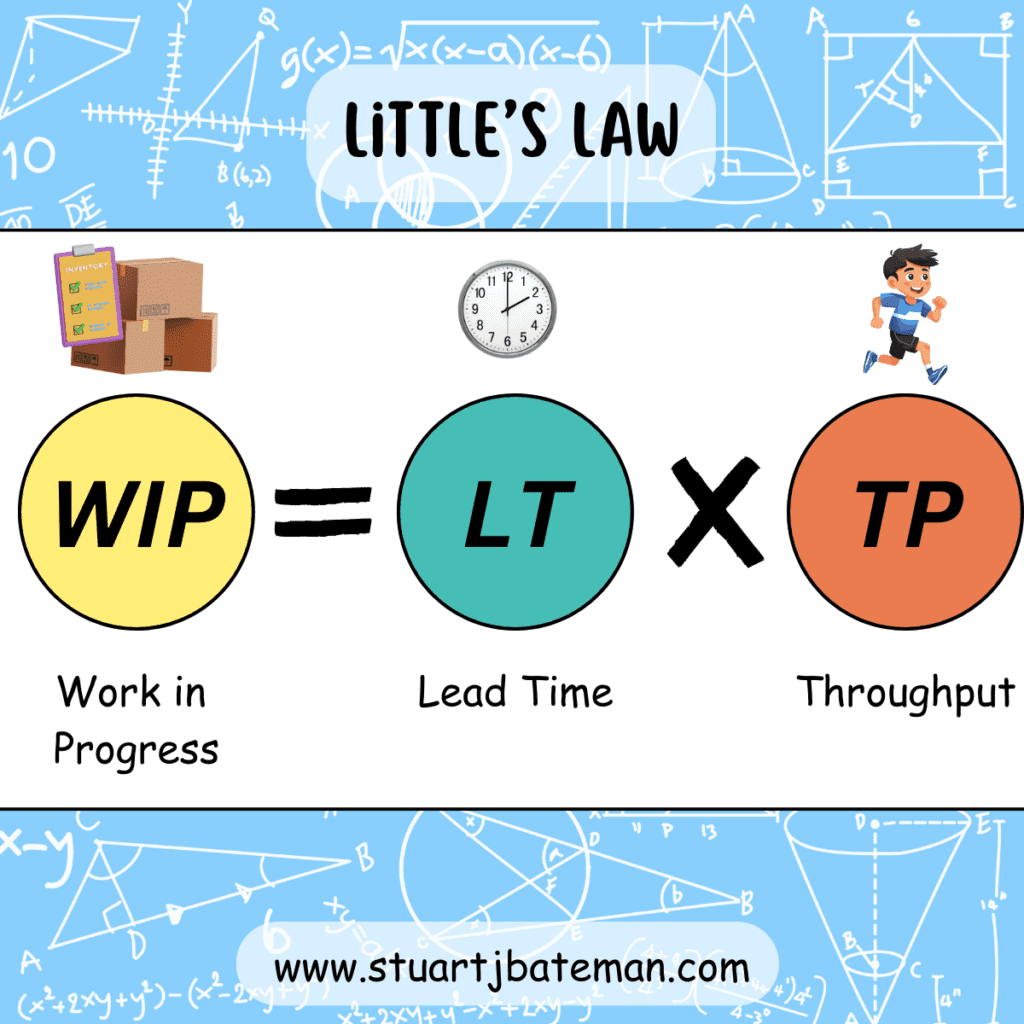
Move onto to implementing the first 3s of those 5 (Sort/Sweep/Shine) into the production area you’re working in or just the lone process and sort out daily used items from everything else and then quarantine the rest to be sorted through (repeaters and strangers – but kept away from process), move on to any jigs / fixtures and gauges the area has and find locations nearby while assessing their condition and if needed refurb or remake them (if there are homemade versions then replace) but remember that all of these need to be drawn up (you be surprised how many companies I’ve been to and work at that hasn’t even done this) so they can be replaced, this decentralises the information (have old Bob retire and no-one knowing how things go together). Clean everything which leads us to repeating the 3s on whatever period you’re happy with which ends up giving you all 5s after writing your procedure of checks…simple. No really.
After which I move on to basic visual management starting with shadow boards and floor markings (keep it simple, just because there’s 7 colours in the rainbow doesn’t mean you have to use them all). Later visual management will be use within TPM / 7QC / SOP’s and H&S.
SOP’s (Standard work procedures) many companies have these in many different forms, from the PC controlled version (which I prefer) to whatever is in Gary’s head who’s been here for the last 30 years. Speak to the operators to find out what’s the best practise (currently), agree on this with all & then update or create paper SOPs to start the continuous improvement process (remember here its best to video process and you’ll find people will forget half the things they do when they think about it and then there’s that – “oh yeah you need to do that to” when they watch the video back). Once you have that bedrock people will find ways to self-optimise and improve on that process, you just need to keep going back to see what ideas they’ve had to improve ‘their’ part. Now with SOP’s they are a pain to maintain (hence go digital) and are mainly used for training as I have yet to come across an operator who sticks rigorously to one, so audit and ask questions every time you visit processes to see what’s changed as people will naturally find the path of least resistance (how true this statement has been in my life since my Electronics classes at College).
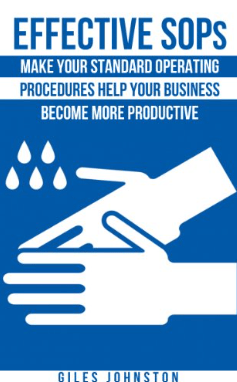
7QC (Quality tools), from the initial set of 7 tools that are available (many more are around today – I can recommend a research paper “Basic Quality Tools in Continuous Improvement Process” – Stronojniski Vestnik 2009) I use SPC / Run charts and tick sheets to start monitoring and managing a process. Here I tip my cap to my colleagues at AI for showing me how pen & paper are truly the wisdom before using money (that and adapting the SPC sheets into a Rocketbook template making in my opinion the ultimate copy & paste SPC solution for no money at all). Operators given enough training and support start to read the data they are producing for you, from this they make simple decisions which benefit the process (one of my main aims is to decentralise decisions or remove them all together so the process becomes black & white. What doesn’t fit is rejected from the system for an engineer to spend time fixing).
Tick sheets are a simple and effective way to get a lot of data, at the same time we can get buy in from the operators. The method I use is to correctly design the sheets where only a few ticks are required, this helps with the counter argument of the time they don’t have when showing them it takes seconds usually does the trick. There is a long-standing culture that any time spend not producing is undesirable (until you tell them that it’s now part of their process to record, as this leads to further improvements. It works both ways, if they want things to change, we need to data to justify/support development).
Lastly TPM (Total Productive / Preventative Maintenance), with the idea of flow discussed earlier the biggest event that can hinder this is a machine breakdown (apart from no resources). I usually leave TPM until last. Why? Because I setup data capture monitoring first to understand the OEE (Overall Equipment Effectiveness) baseline while I work on the other aspects of Lean Manufacturing that we’ve just gone through. We should see a natural improvement of OEE from those efforts. When I get to the TPM stage there is at least 3 months data I can dig through to find quick wins before doing analysis on the rest to find the chronic failures.
After the first improvement round
At this stage you’ve implemented many of the tools used in Lean Manufacturing which allow you to monitor and improve continuously. After a period of time depending on resources / company objectives and other influences you can move onto Pull, but remember to take another snap shot as a benchmark. By this I mean another VSM of the current state so you can discuss with colleagues / managers and operators what processes need to change or implemented to move towards Pull.
This isn’t far off the Womack & Jones Lean Manufacturing method:
- Value
- VSM
- Flow
- Pull
- Perfect
However, I have found that the main challenges and difficulties are within the Flow stage as after you tackle this, most of the obstacles that where embedded in culture start to ease as they see the changes working (but you will need to keep on top of this as it’s human nature to move towards the path of least resistance, people will solve their own problems even if that means the changes what you have done).
So, this is may recommendation (also the route I took), yours could be the same or a variance of it. I would enjoy finding out other people’s approaches and experiences on this topic so please leave a comment below.
The books in this piece are some of the many I have read to enrich and develop myself, check out my current reading list and recommendations at:
Or perhaps you would like to learn more? then I recommend my resources page:
There’s also my Engineer’s Log Book PDF download for £1.99!, get yours here:
Engineer’s Log Book PDF download
What are your thoughts? Have I covered everything or is there more you know and would like to share?
I’m always learning and improving this site and my blogs, so please feel free to get in touch with me via LinkedIn or this site to discuss any topics I have covered.
If you’re having trouble finding ways to progress check out this site filled with free learning tools: